耐熱性(塑料組件)檢測:技術突破與產業(yè)賦能
隨著工業(yè)4.0進程加速,塑料組件在汽車、電子、航空航天等高溫場景的應用比例顯著提升。據中國塑料加工工業(yè)協會2024年報告顯示,耐高溫塑料市場規(guī)模已達320億美元,年復合增長率達8.7%。然而,塑料材料在高溫環(huán)境下易發(fā)生軟化、蠕變、分解等問題,導致產品失效風險。在此背景下,耐熱性(塑料組件)檢測成為保障產品可靠性的關鍵環(huán)節(jié),其核心價值體現在降低質量事故率、優(yōu)化材料選型及延長產品壽命周期三個方面。通過精準的熱穩(wěn)定性評估,企業(yè)可減少因熱失效導致的召回損失,據德國萊茵統(tǒng)計,2023年完善耐熱檢測體系的企業(yè)平均質保成本降低23%。
熱性能檢測技術原理與創(chuàng)新
耐熱性檢測以熱力學分析為核心,涵蓋熱變形溫度(HDT)、維卡軟化點(VST)、熱失重分析(TGA)等關鍵指標。以ASTM D648標準為例,通過三點彎曲法在1.82MPa載荷下測定材料變形量達0.25mm時的溫度閾值。近年發(fā)展的動態(tài)熱機械分析(DMTA)技術可同步監(jiān)測儲能模量、損耗因子等動態(tài)參數,據中國科學院化學研究所2024年研究,該技術對交聯型塑料的熱穩(wěn)定性評估精度提升40%。基于機器學習的預測模型正推動檢測智能化,通過歷史數據訓練可預測新型復合材料的耐熱行為。
全流程檢測實施體系構建
規(guī)范化的檢測流程包含五個階段:首先依據ISO 75-2標準進行樣品預處理,在(23±2)℃、50%RH環(huán)境平衡48小時;其次采用熱流型DSC設備進行玻璃化轉變溫度測定;第三階段執(zhí)行階梯式升溫試驗,以5℃/min速率從室溫升至300℃;第四步通過三維形貌掃描儀量化表面形變;最終結合有限元分析模擬實際工況。某新能源汽車企業(yè)在電池支架檢測中采用此流程,成功將熱變形臨界溫度檢測誤差控制在±1.5℃以內。
行業(yè)應用場景與效益分析
在汽車發(fā)動機艙部件檢測中,高溫環(huán)境下塑料性能檢測技術展現顯著價值。某德系車企對PA66-GF35材質的進氣歧管進行150℃/2000h持續(xù)熱老化測試,通過傅里葉紅外光譜(FTIR)發(fā)現分子鏈斷裂閾值,據此優(yōu)化了玻纖含量配比,使部件耐熱壽命延長30%。電子電器領域則聚焦連接器端子應用,華為2023年導入熱變形溫度測試方法后,5G基站外殼在85℃環(huán)境下的尺寸穩(wěn)定性達到IEC 62137-1 Class 5要求。
標準化質量保障體系演進
行業(yè)正構建四級質量保障機制:實驗室通過ISO/IEC 17025認證確保檢測能力;設備定期進行NIST溯源校準;建立包含287項參數的塑料熱性能數據庫;實施盲樣比對與能力驗證計劃。集團2024年實驗室間比對數據顯示,熱變形溫度測試的實驗室間偏差已從2019年的±4.2℃壓縮至±1.8℃。區(qū)塊鏈技術的引入使檢測數據不可篡改性達到99.99%,顯著提升結果公信力。
展望未來,建議從三方面深化發(fā)展:首先建立跨行業(yè)的熱-力-化多場耦合檢測標準,應對復雜工況需求;其次開發(fā)基于數字孿生的虛擬檢測系統(tǒng),實現全生命周期熱管理;最后加強生物基耐高溫材料的評價體系研究,推動綠色制造轉型。隨著檢測精度突破0.5℃量級,塑料組件的熱可靠性將支撐更多前沿領域的創(chuàng)新應用。

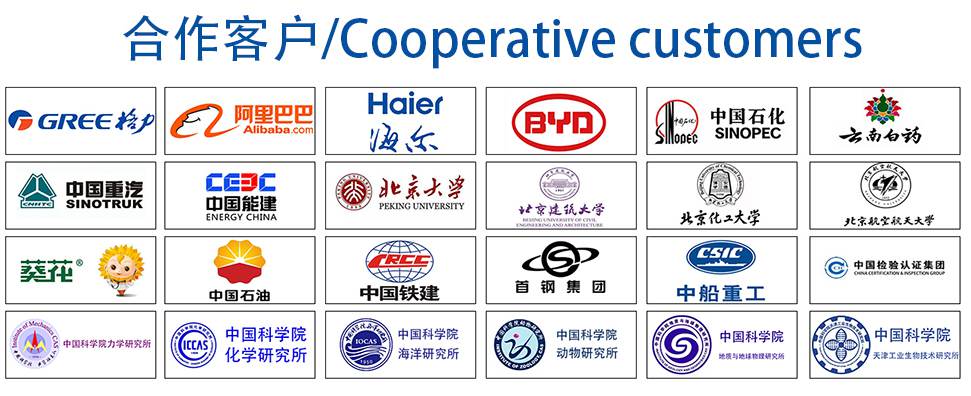