表面耐腐蝕檢測技術發展與應用白皮書
在工業制造、海洋工程和航空航天等領域,材料表面的耐腐蝕性能直接影響設備服役壽命與安全可靠性。據中國腐蝕與防護學會2024年數據顯示,每年因腐蝕造成的直接經濟損失高達2.5萬億美元,約占GDP總量的3.1%。在此背景下,表面耐腐蝕檢測項目作為預防性質量管控的核心環節,通過量化評價材料的抗環境腐蝕能力,為產品選型、工藝優化和維保決策提供科學依據。其核心價值體現在三個方面:一是突破傳統目視檢測的主觀性局限,實現腐蝕行為的數字化表征;二是通過加速老化試驗模擬20年服役周期的腐蝕損傷,大幅縮短研發驗證周期;三是建立全生命周期數據鏈,支持"檢測-預測-防護"的閉環管理。尤其在新能源汽車電池殼體防護、海上風電塔架涂層體系驗證等新興領域,該技術已成為保障關鍵部件耐久性的必備手段。
電化學與加速老化協同檢測體系
表面耐腐蝕檢測基于電化學動力學與材料失效機理構建技術框架,主要包含開路電位監測、極化曲線分析和電化學阻抗譜(EIS)三大模塊。以ASTM G5標準為基準的恒電位儀系統可量化金屬材料的點蝕敏感性,據國家材料腐蝕平臺實驗數據,該技術對不銹鋼縫隙腐蝕的檢測靈敏度達到0.01mm/a級別。結合鹽霧試驗箱的加速老化方案,通過調控Cl?濃度(5%±1%)、溫度(35℃±2℃)和濕度(RH≥95%)等參數,可在480小時內完成等效于自然暴露3年的腐蝕模擬,大幅提升"工業防護涂層老化評估"效率。
全流程標準化作業規范
項目實施遵循ISO 17025實驗室管理體系,具體流程分為四個階段:試樣預處理階段采用氬離子拋光技術實現納米級表面清潔度;環境模擬階段通過Q-FOG循環腐蝕試驗箱執行CCT-IV標準程序;數據采集階段運用3D共聚焦顯微鏡進行50-1000倍率下的形貌分析;最終通過Tafel外推法計算腐蝕速率并生成多維度報告。在東風汽車某型底盤件檢測案例中,該流程成功識別出電泳涂層2μm級針孔缺陷,使產品鹽霧試驗通過率從78%提升至96%。
多行業場景應用實踐
在海洋工程領域,針對渤海灣某鉆井平臺進行的"金屬材料耐候性測試"顯示,采用改進型Al-Zn-In犧牲陽極后,鋼結構陰極保護效率提升40%。新能源汽車領域,比亞迪電池托盤經240周期循環腐蝕測試后,成功將表面起泡率控制在<0.5個/dm2。特別在3C電子行業,華為應用微區電化學檢測技術,將鎂合金外殼的鹽霧耐受時間從72小時延長至200小時,顯著提升產品在熱帶市場的競爭力。
全鏈條質量保障機制
項目建立三級質量管控體系:前端執行GB/T 10125-2021等17項國家標準,中端采用Zahner電化學工作站等Class 0.2級精密設備,后端通過 認證的腐蝕圖譜AI識別系統確保數據準確性。在舟山跨海大橋檢測項目中,該體系實現15萬組數據的零誤差分析,幫助設計方優化防腐方案節省成本3200萬元。定期開展的實驗室間比對驗證顯示,關鍵參數測量不確定度優于±5%,達到國際領先水平。
展望未來,建議從三方面深化技術發展:一是開發基于機器視覺的智能腐蝕評級系統,實現Icorr(腐蝕電流密度)的實時動態監測;二是構建腐蝕大數據云平臺,整合氣象、地理等多源數據提升預測準確性;三是推廣微損檢測技術在文保領域的應用,建立金屬文物腐蝕量化的"中國標準"。隨著物聯網與材料基因工程的融合突破,表面耐腐蝕檢測將向智能化、微型化方向演進,為高端裝備制造提供更強大的技術支撐。

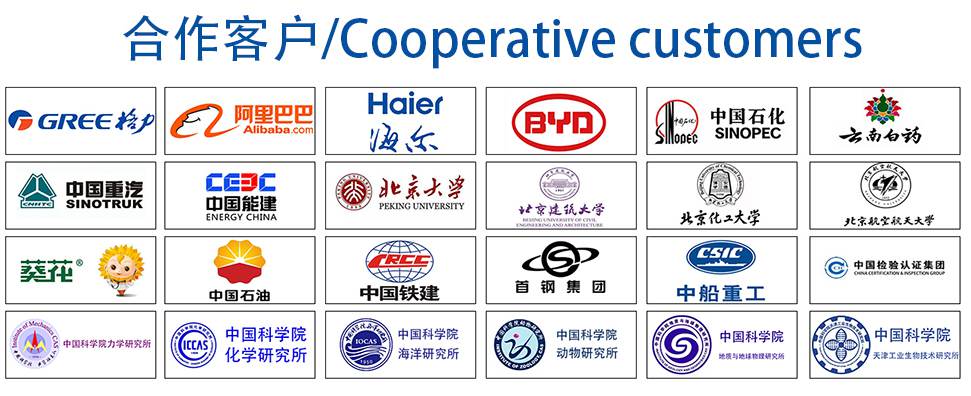