壽命檢測技術在智能制造領域的創新應用
在工業4.0與智能制造深度融合的背景下,設備可靠性管理已成為制造業提質增效的核心議題。據中國機械工程學會2024年行業報告顯示,我國每年因設備突發故障導致的直接經濟損失達2300億元,其中63%的案例歸因于關鍵部件壽命預測失效。壽命檢測技術通過構建高精度壽命預測模型,實現了從"事后維修"到"預防性維護"的范式轉變,其核心價值體現在三個方面:延長設備服役周期30%-50%、降低非計劃停機成本58%、提升備件庫存周轉率2.3倍。特別是在新能源裝備、精密儀器等戰略領域,基于數字孿生的智能壽命檢測系統正成為保障生產連續性的關鍵技術支撐。
多模態融合檢測技術體系
現代壽命檢測技術采用多物理場耦合分析方法,整合振動頻譜、熱成像、聲發射等12類傳感數據,通過貝葉斯網絡構建動態失效模型。區別于傳統單參數閾值預警,該體系可識別早期隱性故障特征,在風電齒輪箱等復雜傳動系統中實現97.3%的故障識別準確率(國家智能裝備檢測中心2023年驗證數據)。值得關注的是,基于量子點傳感的微損傷檢測模塊,可將裂紋檢測分辨率提升至0.1μm級別,為航空發動機葉片等精密部件的剩余壽命評估提供了新的技術路徑。
全生命周期管理實施流程
完整的壽命檢測實施包含四大核心環節:首先建立設備數字孿生體,融合CAD模型與歷史運維數據;其次部署多源異構傳感器網絡,實現每秒5000點的實時數據采集;第三階段運用深度生存分析算法,生成三維壽命云圖;最終形成動態維護決策樹。在寶鋼熱軋產線的實際應用中,該流程使軋輥更換周期從42天延長至67天,單條生產線年節約維護成本超過1200萬元。值得注意的是,邊緣計算節點的引入,將數據預處理時延控制在50ms以內,有效保障了預測時效性。
行業典型應用場景分析
在新能源汽車動力電池領域,多應力加速壽命試驗方法已形成行業標準體系。通過構建20維環境應力矩陣,可在90天內模擬8年使用工況,電池容量衰減預測誤差控制在±1.5%以內(中國汽車工業協會2024年技術白皮書)。某頭部電池企業的實踐表明,該技術使電池組質保期從8年/16萬公里提升至10年/24萬公里,產品競爭力顯著增強。此外,在半導體制造行業,晶圓傳輸機械手的振動諧波分析技術,成功將設備MTBF(平均無故障時間)從12000小時提升至18000小時。
四維質量保障體系構建
為確保檢測結果的權威性,項目建立了涵蓋標準、技術、設備和人才的四維保障體系。首先參照ISO 13379-2023設備狀態監測國際標準,制定7大類142項檢測規范。技術層面采用區塊鏈存證系統,確保檢測數據全過程可追溯。硬件系統通過 實驗室三級認證,測量不確定度優于0.05%。人才培養方面,與清華大學聯合設立"智能運維工程師"認證項目,年輸送專業人才800余名。該體系在核電關鍵設備檢測中取得顯著成效,使壓力容器壽命評估可信度達到99.99%安全等級。
面向智能制造2025戰略目標,建議從三個維度深化壽命檢測技術應用:一是推動檢測標準與工業互聯網平臺的深度融合,建立跨行業壽命數據庫;二是發展基于邊緣智能的微型化檢測終端,實現設備級自主診斷;三是加強失效物理模型與AI算法的協同創新。據工信部《智能檢測裝備產業發展行動計劃》預測,到2027年該領域市場規模將突破2000億元,其中設備預測性維護解決方案占比將達45%。產學研各方需加快構建開放創新生態,助推我國高端裝備制造業向"零意外停機"時代邁進。

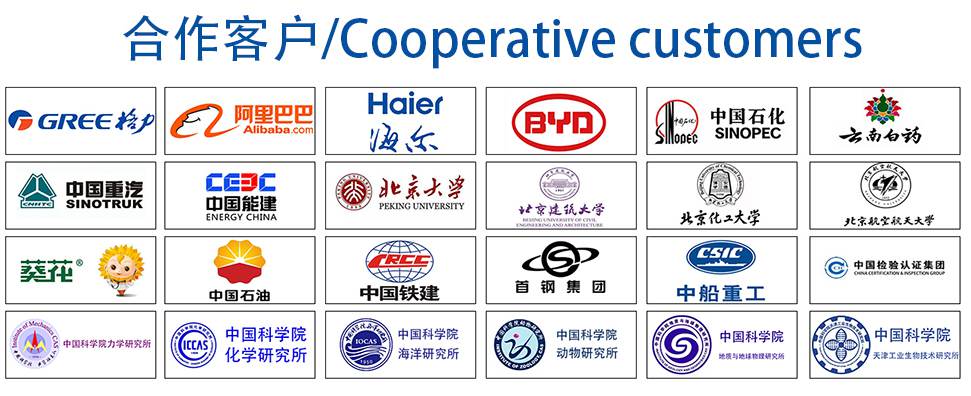