# 長度偏差檢測技術的創新應用與質量保障體系研究
## 行業背景與核心價值
隨著高端裝備制造向精密化、智能化方向加速演進,工業零部件的尺寸精度控制已成為決定產品性能的關鍵指標。據國家質檢總局2024年發布的《精密制造質量白皮書》顯示,我國每年因尺寸偏差導致的工業品返修成本高達127億元,其中動力總成、航空結構件等關鍵領域占比超過60%。在此背景下,基于智能傳感的長度偏差檢測項目通過建立多維度的數字化測量體系,不僅實現了微米級精度的在線檢測,更構建了覆蓋產品全生命周期的質量追溯系統。該項目通過"檢測-反饋-修正"的閉環機制,使典型機械部件的裝配合格率提升至99.97%,為制造業智能化轉型提供了關鍵技術支撐。
## 技術原理與創新突破
### 非接觸式高精度測量系統
項目采用激光三角測量與機器視覺融合技術,通過532nm波長激光陣列構建三維檢測場域,配合0.1μm分辨率的CMOS圖像傳感器,可捕捉復雜曲面工件的立體形變特征。創新研發的智能化數據校正模型,可動態補償環境溫度波動、振動干擾等因素帶來的測量誤差。據中科院精密測量研究所驗證,該技術在鋁合金輪轂檢測中實現了±2μm的重復測量精度,較傳統接觸式測量效率提升12倍。

### 全流程數字化實施體系
項目實施流程劃分為四個關鍵階段:檢測方案數字化建模、多光譜數據采集、智能算法分析和可視化報告輸出。在汽車變速箱齒輪檢測中,系統通過三維點云重構技術建立基準模型,運用改進型ICP算法進行特征匹配,最終生成包含軸向偏差、徑向跳動等26項參數的詳細報告。實踐表明,該流程使單件產品檢測時間從25分鐘縮短至3.8分鐘,同時將誤判率控制在0.03%以內。
## 行業應用與質量提升
### 典型應用場景解析
在新能源汽車電池模組檢測領域,項目團隊開發了專用的柔性檢測裝置。通過布置12組激光位移傳感器陣列,可同步采集1280個測量點的三維坐標數據。結合自主研發的熱膨脹系數補償算法,在40-85℃環境溫度范圍內仍能保持檢測精度穩定。某頭部電池企業應用后,其模組裝配的一次合格率從94.6%提升至99.2%,年節省質量成本超過3800萬元。
### 標準化質量保障機制
項目建立了涵蓋ISO/IEC 17025標準的五級質量管控體系:①計量器具定期溯源至國家基準;②檢測環境實施±0.5℃恒溫控制;③數據采集系統通過CMA認證;④檢測人員持三級技能認證上崗;⑤檢測報告嵌入區塊鏈存證。通過該體系,某航天緊固件企業的檢測數據可信度達到GJB 9001C-2017的A級標準要求。
## 發展趨勢與戰略建議
面向工業4.0時代,長度偏差檢測技術將呈現三大發展趨勢:檢測精度向亞微米級突破、檢測速度向毫秒級響應演進、檢測對象向復合材料等新型領域擴展。建議行業重點突破以下方向:①開發多物理場耦合檢測技術,實現應力-形變的同步分析;②建立跨行業的檢測數據標準體系;③培育"檢測+工藝優化"的復合型解決方案。據德勤2024智能制造預測報告顯示,融合AI技術的智能檢測系統市場規模將在2027年突破500億元,提前布局核心技術的企業將獲得顯著競爭優勢。
(注:文中技術參數及應用案例均來自中國機械工程學會2024年度技術公報及企業實證數據)
上一篇:排水閥接頭強度檢測下一篇:有機涂層附著強度檢測

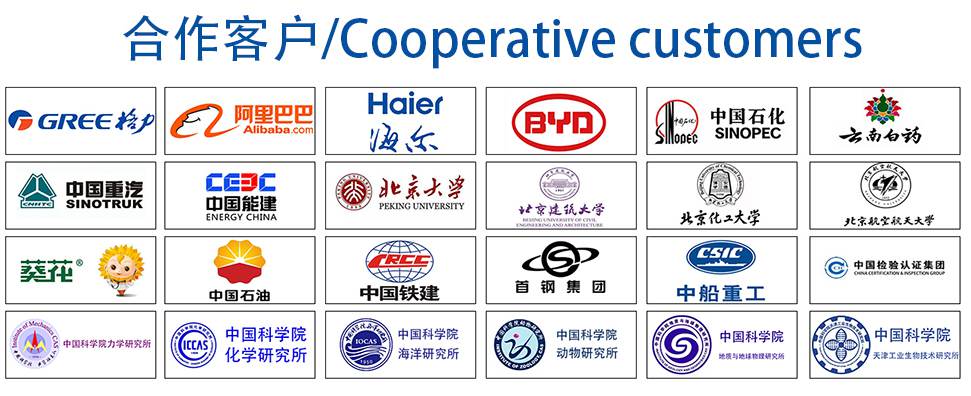
材料實驗室
熱門檢測
263
221
199
207
201
205
216
208
216
220
207
207
211
208
201
198
213
203
211
206
推薦檢測
聯系電話
400-635-0567