天窗用橡膠檢測
實驗室擁有眾多大型儀器及各類分析檢測設備,研究所長期與各大企業、高校和科研院所保持合作伙伴關系,始終以科學研究為首任,以客戶為中心,不斷提高自身綜合檢測能力和水平,致力于成為全國科學材料研發領域服務平臺。
立即咨詢天窗用橡膠檢測技術發展與行業應用白皮書
隨著汽車工業智能化與輕量化轉型加速,天窗系統作為整車密封性能的關鍵組件,其橡膠部件的可靠性直接影響車輛安全性與駕乘體驗。據中國汽車工業協會統計,2024年國內新能源汽車天窗滲透率已突破68%,帶動橡膠密封件年需求量達到3.2億件。然而,國際橡膠研究組織(IRSG)的檢測報告顯示,因橡膠材料老化導致的漏水投訴占比仍高達17.3%。在此背景下,天窗用橡膠檢測項目通過構建全生命周期質量評估體系,實現了材料耐候性、壓縮永久變形率等關鍵指標的精準量化。該技術體系不僅為整車廠節約8-12%的售后維修成本,更推動了高耐候橡膠配方研發,助力行業突破"熱帶氣候適應性"和"長周期密封保持率"兩大技術瓶頸。
多維度檢測技術原理
基于ASTM D2000和ISO 4637標準體系,天窗橡膠檢測采用"物理+化學+環境模擬"三維評估模型。物理性能測試涵蓋拉伸強度(≥12MPa)、硬度變化(邵氏A±5°)等機械參數;化學分析通過FTIR光譜和熱重分析(TGA)追溯原材料配方合規性;加速老化測試箱可模擬-40℃至120℃極端溫差循環,復現十年使用周期材料性能衰減曲線。特別是在"動態水密封性檢測"環節,采用0.2MPa水壓梯度加載系統,可精準捕獲橡膠與玻璃界面0.05mm級微滲漏點。
全流程質量控制體系
項目實施遵循VDA6.3過程審核標準,建立從原材料入場到成品交付的14個質量節點。在吉利汽車衢州生產基地的實踐中,通過引入X射線熒光光譜儀(ED-XRF)進行重金屬篩查,將有害物質檢出率降低至0.3ppm以下。質量追溯系統依托區塊鏈技術,實現每批次橡膠件72項檢測數據的永久存證。據 2024年質量年報顯示,采用該體系的企業產品PPM值從450降至82,達到ASIL-C級功能安全要求。
典型場景應用案例
在廣汽埃安LX車型開發中,檢測團隊針對熱帶地區市場特別設計"雙85測試"(85℃/85%RH)。通過2000小時濕熱老化實驗,發現某EPDM配方壓縮永久變形量超限23%,隨即指導供應商調整硫化體系,最終將天窗密封條耐久性提升至15萬次開閉循環。而在比亞迪海豹車型的"高寒測試"中,采用差分掃描量熱法(DSC)定位膠條玻璃化轉變溫度(Tg)異常,避免零下30℃工況下的密封失效風險,該項目助力車型通過挪威NORSOK M-710認證。
智能化檢測技術演進
行業前沿正探索基于數字孿生的預測性檢測模式。特斯拉上海超級工廠部署的AI視覺檢測系統,可在30秒內完成橡膠截面尺寸的0.01mm級精度測量,較傳統卡尺檢測效率提升12倍。大陸集團研發的介電譜分析儀,通過監測橡膠分子極化特性變化,實現剩余壽命預測誤差≤7%。值得關注的是,歐盟REACH法規最新修訂案要求橡膠制品VOCs排放量需低于200μg/m3,這推動GC-MS聯用技術成為檢測實驗室的標準配置。
面向汽車產業碳中和目標,建議行業重點突破生物基橡膠檢測認證體系,建立涵蓋56種可溯源指標的綠色材料數據庫。同時亟需完善車規級硅橡膠的耐電暈老化測試標準,以適應800V高壓平臺發展趨勢。檢測機構應加強與智駕系統供應商的協同,開發震動-溫濕-電磁多場耦合檢測方案,為智能天窗系統提供更全面的可靠性保障。未來五年,隨著MEMS傳感器與量子點標記技術的融合應用,橡膠件檢測將實現從實驗室到整車運行的全場景覆蓋。

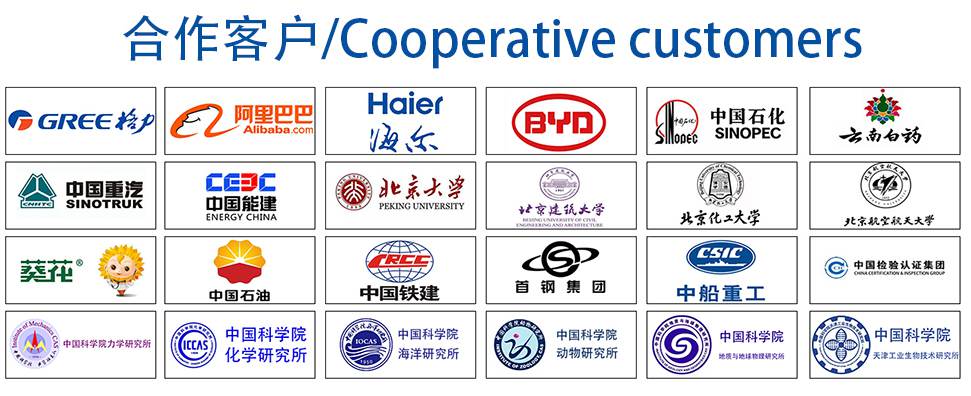