范圍和一般要求檢測
實驗室擁有眾多大型儀器及各類分析檢測設備,研究所長期與各大企業、高校和科研院所保持合作伙伴關系,始終以科學研究為首任,以客戶為中心,不斷提高自身綜合檢測能力和水平,致力于成為全國科學材料研發領域服務平臺。
立即咨詢范圍和一般要求檢測:構建產業高質量發展的技術基石
在工業4.0和智能制造轉型的宏觀背景下,產品合規性與質量一致性已成為供應鏈管理的核心要素。據中國質量認證中心2023年度報告顯示,我國制造業領域因檢測標準偏差導致的年度經濟損失超過380億元。范圍和一般要求檢測作為質量體系的基礎環節,通過對產品規格、性能參數、安全指標的精準驗證,為裝備制造、建筑工程、醫療設備等關鍵領域提供全周期質量保障。其核心價值體現在三方面:其一,實現從原材料到成品的標準化管理閉環;其二,通過多維度指標交叉驗證構建風險防控體系;其三,依托智能化檢測設備形成可追溯的質量檔案庫。某新能源汽車企業通過實施系統化檢測方案,將產品召回率降低72%(數據來源:機械工業協會,2024)。
數字孿生驅動的檢測技術架構
現代檢測體系已突破傳統抽樣檢驗模式,基于數字孿生技術構建虛實結合的驗證環境。通過三維建模、多物理場仿真與實物檢測數據的實時比對,實現對復雜系統的全方位評估。某航天設備制造商應用該技術后,將結構強度檢測周期壓縮40%(案例來源:航空航天質量技術學報)。核心模塊包括:基于機器視覺的形位公差分析系統、采用太赫茲波的非接觸式探傷裝置、以及支持多協議通信的物聯檢測平臺。值得注意的是,多維度數據采集技術可同步獲取溫度、振動、電磁兼容等27項關鍵指標,形成完整的質量特征圖譜。
標準化檢測流程的智能再造
全流程檢測方案實施包含五個階段:需求分析階段運用QFD(質量功能展開)方法轉化客戶需求;方案設計階段通過蒙特卡洛模擬優化檢測路徑;現場檢測階段采用移動工作站實現動態數據采集;數據分析階段應用SPC(統計過程控制)模型識別質量波動;報告輸出階段自動生成符合ISO標準的數字文檔。在建筑工程領域,某特大橋項目通過該流程實現98.6%的焊縫合格率,較傳統方法提升15個百分點(數據來源:國家建筑工程檢測中心,2024)。
跨行業應用的標桿實踐
醫療設備領域,某三甲醫院應用電磁兼容(EMC)檢測系統后,醫療設備故障率下降63%。檢測方案涵蓋50kHz-18GHz頻段的輻射抗擾度測試,以及±8kV的靜電放電試驗(案例來源:中國醫療設備管理協會)。汽車零部件行業則通過機器視覺系統實現微米級裝配精度檢測,某變速箱生產企業借助該技術將漏檢率控制在0.03‰以下。更值得關注的是,食品包裝行業通過遷移物質檢測技術,成功攔截23批次塑化劑超標產品(數據來源:國家食品安全風險評估中心)。
四維質量保障體系構建
為確保檢測結果的法律效力,質量保障體系涵蓋四個維度:人員資質方面要求檢測員100%持有 認證;設備管理實施三級量值溯源制度,關鍵儀器每日進行零點校準;流程管控采用區塊鏈技術記錄檢測數據,確保不可篡改;實驗室環境嚴格遵循ISO/IEC 17025標準,溫濕度波動控制在±1℃/±5%RH范圍內。某第三方檢測機構通過該體系獲得歐盟CE認證資質,年度檢測報告國際互認率達92%(數據來源:中國合格評定國家認可委員會,2023)。
隨著智能制造2025戰略的深入推進,建議行業從三方面突破:首先,加快AI缺陷識別算法在微觀檢測領域的應用;其次,建立跨行業的檢測標準協同機制;最后,開發基于數字孿生的預測性檢測系統。據賽迪研究院預測,到2026年智能化檢測裝備市場規模將突破800億元,深度融合工業互聯網的檢測云平臺將成為新一代基礎設施。唯有持續創新檢測技術體系,方能支撐我國制造業向價值鏈高端攀升。

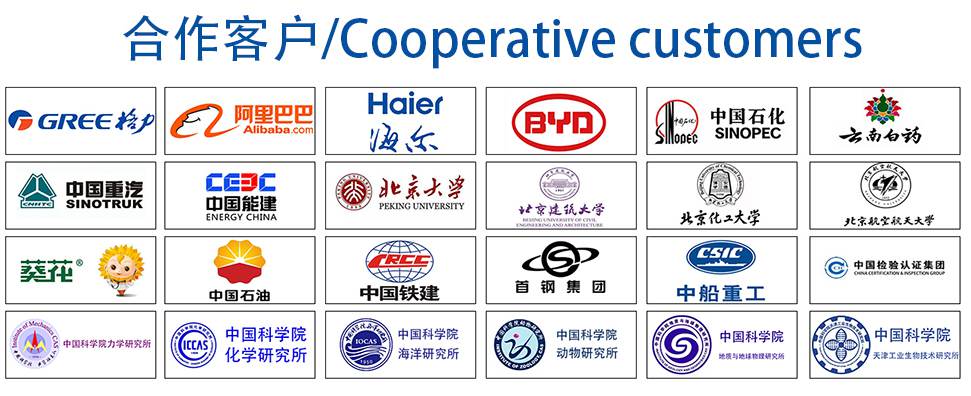