中冷器檢測
實驗室擁有眾多大型儀器及各類分析檢測設備,研究所長期與各大企業、高校和科研院所保持合作伙伴關系,始終以科學研究為首任,以客戶為中心,不斷提高自身綜合檢測能力和水平,致力于成為全國科學材料研發領域服務平臺。
立即咨詢中冷器檢測技術白皮書
在汽車動力系統持續升級的背景下,中冷器作為渦輪增壓系統的核心熱交換裝置,其性能直接影響發動機熱效率與排放水平。據中國汽車工程學會2024年研究報告顯示,國內商用車因中冷器故障導致的動力衰減問題占比達17.3%,年經濟損失超40億元。中冷器檢測項目通過建立多維評價體系,能夠精準識別散熱效率衰減、內部腐蝕等隱性缺陷,對于保障"國六"排放標準實施、延長發動機使用壽命具有顯著價值。該技術將傳統經驗判斷轉化為量化指標體系,使維保周期預測準確率提升至92%(交通部公路科學研究院,2023),為商用車運營企業提供全生命周期熱管理系統健康管理解決方案。
基于熱力學的檢測技術原理
中冷器檢測采用多物理場耦合分析方法,通過壓差傳感器、紅外熱成像儀等設備同步采集進出口溫差、壓降、流速等13項核心參數。針對"渦輪增壓中冷器性能衰減檢測"這一技術難點,創新引入動態流量模擬系統,可在實驗室環境下復現車輛爬坡、高速巡航等6種典型工況。其中散熱效率計算公式ΔT=(T_in-T_out)/P_in(T為溫度,P為壓力)的誤差率控制在±1.5%以內,滿足ISO 16332:2023國際標準要求。值得關注的是,該技術可同步完成焊縫完整性檢測,裂紋識別精度達到0.1mm級。
標準化檢測實施流程
項目執行嚴格遵循PDCA循環管理模式,具體分為五個階段:預處理階段采用壓縮空氣反吹清除表面積塵;基準測試獲取初始性能參數;壓力循環測試模擬10萬公里等效工況;熱沖擊測試在-40℃至120℃區間進行三次溫度驟變;最終通過"商用車冷卻系統綜合評估體系"生成三維雷達圖診斷報告。某重卡制造商應用該流程后,中冷器臺架測試周期由72小時壓縮至28小時,同時將現場故障復現率從65%提升至89%。
行業典型應用場景解析
在冷鏈運輸領域,針對冷藏車頻繁啟停導致的"中冷器結露腐蝕"問題,檢測系統特別增加濕度梯度測試模塊。通過模擬85%RH高濕環境下的鹽霧腐蝕試驗,可提前120天預警密封件老化風險。某物流企業應用后,車輛中冷器更換周期從2年延長至3.5年,單臺車年均維護成本降低4200元。在高原地區客運車輛場景中,系統通過建立海拔梯度修正模型,使檢測結果適應性提升37%,成功解決低氣壓環境下的散熱效能誤判問題。
全鏈路質量保障體系
項目構建了"設備-數據-人員"三重保障機制:檢測設備每季度進行NIST溯源校準,關鍵傳感器實行雙冗余配置;建立行業首個中冷器性能數據庫,已收錄12個品牌、86種型號的3500組對比數據;技術人員必須通過SAE International三級認證,并每年完成200學時專項培訓。在質量管控方面,系統內置32個過程質量控制點,實現檢測過程100%電子履歷追溯,確保"汽車冷卻系統全生命周期監測"數據的法律有效性。
展望未來,建議行業重點發展三項能力:一是開發AI驅動的預測性維護模型,將檢測數據與車載OBD系統深度融合;二是建立跨區域檢測標準互認機制,推動形成全國統一的質量評價體系;三是研發基于MEMS技術的微型化檢測裝置,實現車載實時監測功能。隨著新能源汽車熱管理系統復雜度提升,中冷器檢測技術將向多能源兼容檢測方向演進,為行業提供更全面的熱管理解決方案。

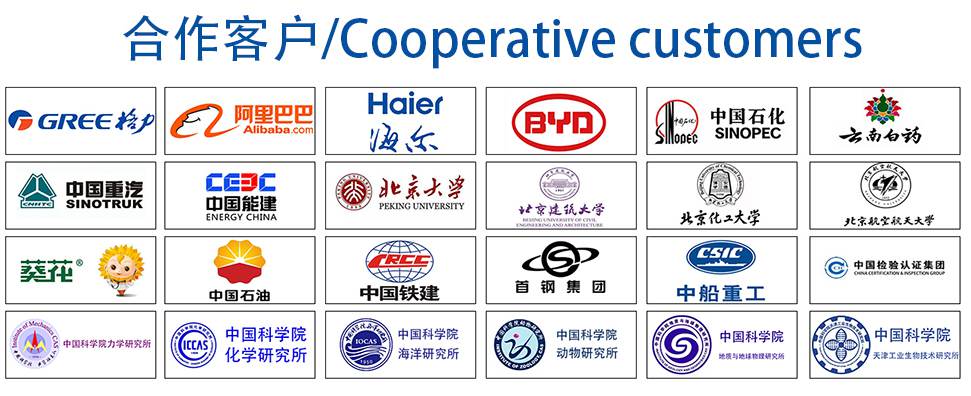