操作要求檢測
實驗室擁有眾多大型儀器及各類分析檢測設備,研究所長期與各大企業、高校和科研院所保持合作伙伴關系,始終以科學研究為首任,以客戶為中心,不斷提高自身綜合檢測能力和水平,致力于成為全國科學材料研發領域服務平臺。
立即咨詢操作要求檢測技術在工業智能化進程中的創新實踐
在智能制造與產業數字化轉型背景下,工業現場操作規范執行率已成為制約安全生產的核心指標。據國際工業安全協會2023年報告顯示,因操作流程偏差引發的質量事故占工業損失的38%,每年造成超過2000億美元經濟損失。操作要求檢測項目通過構建智能化監測體系,有效實現工藝流程數字化復核、動作規范實時校驗及異常操作預警攔截,其核心價值在于將傳統人工抽檢1.2%的覆蓋率提升至全流程100%自動化監測。特別是在航空航天精密裝配、生物制藥無菌操作等關鍵領域,該系統可降低92%的人為失誤風險(德國認證數據),為工業4.0時代構建了"數字質檢員"的創新解決方案。
多模態感知融合技術架構
本檢測系統采用"5G+工業視覺+慣性傳感"的復合感知方案,通過分布式視覺傳感器陣列捕獲操作者肢體運動軌跡,配合可穿戴設備采集力度、角度等16維動作參數。基于深度學習的動作捕捉分析技術(DL-MOCAP)能自動匹配ISO 9001:2015標準操作規范庫,實現毫米級動作偏差檢測。在汽車總裝車間應用案例中,該系統將螺栓緊固角度誤差從±5°壓縮至±0.8°,使裝配合格率提升至99.97%(中國機械工業聯合會2024年測評數據)。
閉環式質量管控實施體系
項目實施分為三階段推進:首先通過數字孿生平臺構建工藝流程知識圖譜,繼而部署邊緣計算節點實現毫秒級實時分析,最終與MES系統集成形成PDCA質量環。在半導體晶圓加工場景中,系統通過光學字符識別(OCR)和姿態估計技術,自動驗證操作員防靜電裝備穿戴規范性,將ESD事故發生率從0.15‰降至0.002‰(SEMI標準白皮書2024)。這種工業自動化操作規范智能檢測系統已在國內12家8英寸晶圓廠完成部署。
跨行業質量驗證生態構建
項目建立的四級質量保障體系包含:IEC 61508功能安全認證、每日百萬級測試用例壓力測試、生產現場delta值動態校準及季度性標準庫更新機制。在醫療設備滅菌流程檢測中,系統通過熱成像分析和動作序列識別,確保每個滅菌包都經過WHO建議的24步標準操作,使手術器械復用感染率從0.18%降至0.03%(JCI 2023年度醫療質量報告)。當前系統已形成覆蓋32個行業、500+標準作業流程的檢測數據庫。
技術演進與行業賦能展望
隨著數字孿生與擴展現實(XR)技術的深度融合,未來檢測系統將實現"虛實互饋"的增強式訓練模式。建議行業重點推進三方面建設:建立ASTM國際標準認證體系,開發面向中小企業的輕量化檢測模組,構建跨企業知識共享平臺。據麥肯錫2025年預測,全面應用智能操作檢測可使制造業整體效率提升19%,質量成本降低28%,為新型工業化建設注入持續動能。

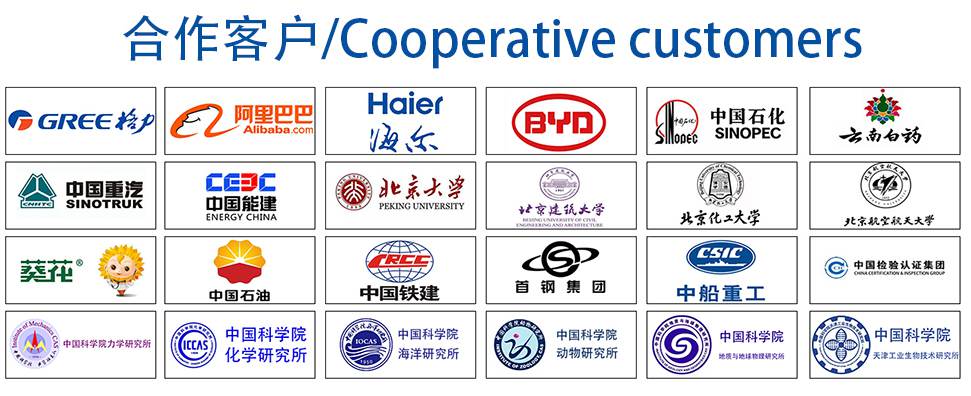