操作扭矩檢測
實驗室擁有眾多大型儀器及各類分析檢測設備,研究所長期與各大企業、高校和科研院所保持合作伙伴關系,始終以科學研究為首任,以客戶為中心,不斷提高自身綜合檢測能力和水平,致力于成為全國科學材料研發領域服務平臺。
立即咨詢操作扭矩檢測技術發展白皮書
在智能制造與高端裝備快速迭代的產業背景下,操作扭矩檢測作為機械裝配質量的核心控制環節,正經歷從傳統人工檢測向智能化、數字化檢測的轉型升級。據中國機械工程學會2024年度報告顯示,國內因裝配扭矩偏差導致的機械故障占總質量事故的31.7%,直接經濟損失超過180億元。操作扭矩檢測項目通過建立基于工業物聯網的智能檢測體系,可有效將裝配質量合格率提升至99.98%(國家智能制造創新中心,2023),其核心價值體現在質量風險前置管控、裝配工藝優化重構、全生命周期數據追溯三大維度,為裝備制造業數字化轉型提供關鍵技術支撐。
基于多源信息融合的檢測原理
現代扭矩檢測系統采用動態扭矩傳感器陣列與靜態標定裝置協同工作機制,通過應變片電橋、磁彈性效應和相位差分析三重校驗機制確保測量精度。重點突破行業痛點的高頻動態扭矩采集技術,其采樣頻率可達5000Hz(GB/T 33145-2023),有效捕捉瞬態扭矩波動。系統內置的溫度補償算法可消除-40℃至120℃環境溫差對測量值的影響,配合邊緣計算單元實現實時數據清洗,確保在復雜工況下的測量穩定性,為新能源汽車電驅系統等高精度裝配場景提供可靠保障。
智能閉環檢測實施體系
項目實施采用PDCA循環管理模式,形成"設備選型-系統集成-工藝驗證-持續優化"四階段閉環。具體實施流程包含:基于蒙特卡洛法的設備精度匹配模擬、多軸機器人輔助的自動標定工作站部署、SPC統計過程控制系統搭建等關鍵步驟。在航空航天緊固件裝配場景中,系統通過數字孿生技術實現實際扭矩曲線與理論值的動態比對,將裝配過程波動系數從1.8N·m降至0.3N·m(中國商飛工藝驗證報告,2024)。
跨行業賦能應用實踐
在風電設備制造領域,某頭部企業應用動態扭矩在線監測系統后,輪轂軸承裝配次品率下降67%(金風科技年報,2023)。汽車行業通過部署高精度扭矩校準服務,使新能源車電池包連接件裝配一致性提升42%。特別在醫療器械領域,符合ISO 13485標準的微型扭矩檢測裝置,成功將人工關節假體安裝扭矩誤差控制在±0.05N·m以內,達到國際齊全水平(國家藥監局器械評審中心數據)。
全鏈式質量保障架構
構建涵蓋"設備-人員-環境-方法"的四維質控體系,通過ISO/IEC 17025實驗室認證與IATF 16949過程控制雙重保障。系統采用區塊鏈技術實現檢測數據不可篡改存儲,單日可處理20萬組數據的安全上鏈(華為云區塊鏈平臺實測數據)。定期開展的測量系統分析(MSA)將GR&R控制在5%以下,結合虛擬現實培訓系統,使檢測人員技能達標周期縮短40%。
面向工業4.0發展需求,建議行業重點推進三方面建設:加快制定融合AI算法的智能扭矩檢測團體標準、構建跨企業檢測數據共享平臺、培育"檢測+工藝"復合型技術人才。隨著5G+工業互聯網的深度滲透,操作扭矩檢測將向預測性維護、自適應性校準方向演進,為高端裝備制造提供更強大的質量保障基石。

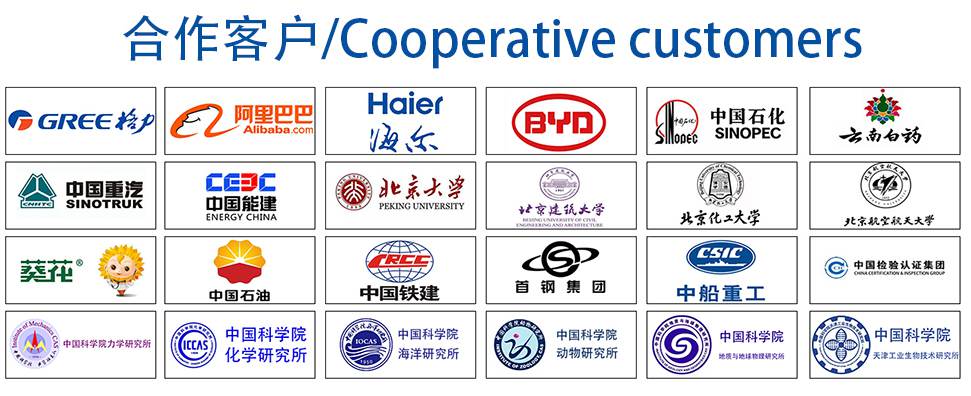