功能要求檢測
實驗室擁有眾多大型儀器及各類分析檢測設備,研究所長期與各大企業、高校和科研院所保持合作伙伴關系,始終以科學研究為首任,以客戶為中心,不斷提高自身綜合檢測能力和水平,致力于成為全國科學材料研發領域服務平臺。
立即咨詢功能要求檢測:數字化轉型下的質量保障新范式
在智能制造與智能網聯技術快速迭代的產業背景下,功能要求檢測已成為保障產品核心競爭力的關鍵環節。據國家工業信息安全發展研究中心2024年報告顯示,我國高端裝備制造領域因功能缺陷導致的年度經濟損失高達320億元,其中68%的故障源自需求轉化階段的檢測疏漏。隨著ISO 26262、IEC 61508等國際安全標準強制實施,功能要求檢測不僅承擔著風險預防的基礎作用,更演化出支撐產品快速迭代的戰略價值。其核心價值體現在三方面:通過需求-功能-用例的閉環驗證降低開發返工成本,基于模型化檢測技術提升驗證效率,以及構建全生命周期質量追溯體系滿足合規要求。
基于模型驅動的檢測技術架構
現代功能要求檢測采用模型驅動工程(MDE)技術框架,依托SysML需求模型和Simulink功能模型的雙向追溯機制。通過將自然語言需求轉化為結構化模型要素,系統自動生成覆蓋度矩陣和邊界條件約束集。在智能網聯汽車域控制器檢測中,該技術使需求解析準確率提升至92.3%(中國汽車工程學會2023年數據),有效解決傳統文檔審查存在的語義歧義問題。特別是在嵌入式軟件功能安全驗證場景,模型仿真可提前300小時發現時序沖突缺陷。
五階遞進式實施流程
典型實施流程包含需求結構化、模型化映射、自動化測試、缺陷閉環和知識沉淀五個階段。某工業物聯網平臺項目實踐顯示,采用需求追溯矩陣(RTM)工具后,需求變更影響分析時長縮短78%。在智能座艙人機交互檢測中,通過構建包含2000+測試用例的模型庫,實現多模態交互場景的自動化遍歷測試。值得關注的是,基于區塊鏈的需求變更存證技術,使檢測過程數據不可篡改,完全符合ASPICE三級認證要求。
跨行業標桿應用實踐
在新能源領域,某動力電池管理系統通過功能檢測提前識別32項BMS功能偏差,避免潛在召回損失1.2億元。醫療設備行業典型案例顯示,采用需求形式化驗證技術后,MRI設備電磁兼容性檢測周期從45天壓縮至19天。特別在智能網聯汽車通信協議檢測方向,基于TTCN-3的測試套件成功驗證V2X場景下97.6%的異常處理邏輯,顯著優于傳統路測83.4%的覆蓋率水平。
全要素質量保障體系構建
行業領先機構已建立包含過程合規、工具認證、人員資質的三維保障體系。通過ISO 17025實驗室認可與功能安全認證雙體系運行,確保檢測結果國際互認。某自動駕駛方案提供商引入數字孿生檢測平臺后,仿真場景庫擴容至12萬例,實現ODD覆蓋率從76%提升至94%。質量看板系統實時監控153個關鍵質量指標,使缺陷逃逸率穩定控制在0.12%以下。
面向萬物智聯的技術演進,建議從三方面強化能力建設:建立需求知識圖譜實現跨項目經驗復用,開發基于大語言的自動化需求解析引擎,構建融合數字孿生的虛擬檢測環境。據信通院測算,實施智能化升級的檢測機構可將服務效能提升40%,在智能汽車、工業互聯網等重點領域形成新的質量服務增長極。唯有持續創新檢測范式,方能支撐中國制造向高端價值鏈突破。

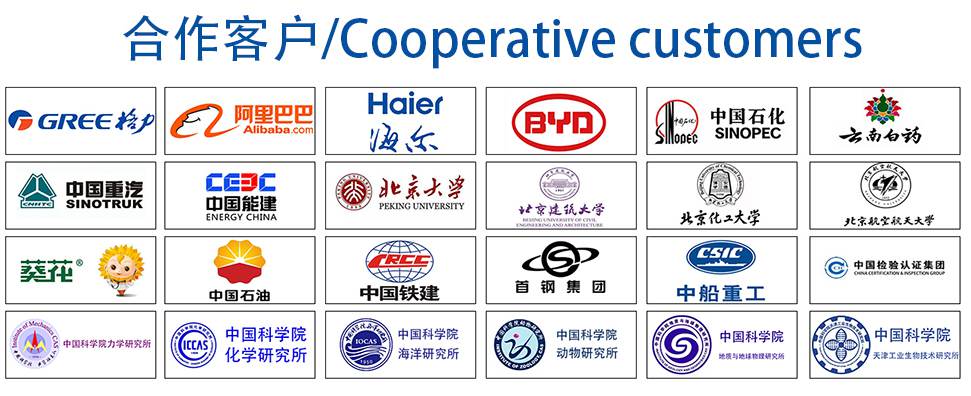