球形連接搖擺性能試驗檢測
實驗室擁有眾多大型儀器及各類分析檢測設備,研究所長期與各大企業、高校和科研院所保持合作伙伴關系,始終以科學研究為首任,以客戶為中心,不斷提高自身綜合檢測能力和水平,致力于成為全國科學材料研發領域服務平臺。
立即咨詢球形連接搖擺性能試驗檢測技術白皮書
在高端裝備制造領域,球形連接件作為關鍵運動部件,其動態性能直接影響機械系統的可靠性與使用壽命。據中國機械工業聯合會2023年行業報告顯示,工程機械、航空航天設備中32%的機械故障源于連接機構失效,其中球形關節類故障占比達17%。在此背景下,球形連接搖擺性能試驗檢測項目通過模擬實際工況下的多維度運動載荷,為產品設計驗證和缺陷診斷提供科學依據。該項目不僅填補了傳統靜態測試無法評估動態疲勞特性的技術空白,更能通過量化分析擺動角度衰減率、接觸面應力分布等關鍵指標,實現產品壽命預測精度提升40%以上,具有顯著的質量控制價值和經濟效益。
多軸耦合加載測試原理
基于六自由度運動平臺與液壓伺服系統的協同控制,試驗系統可復現X-Y-Z三軸空間復合運動。通過集成非接觸式激光位移傳感器(測量精度±0.01mm)和動態扭矩傳感器(量程0-5000Nm),實時采集擺角波動幅度和摩擦扭矩變化曲線。值得關注的是,系統獨創的變溫控制模塊可在-60℃至150℃環境溫度下進行高頻次搖擺測試,精準模擬極寒地區工程機械與航天器艙外機構的實際工況。
標準化檢測流程構建
實施過程嚴格遵循ASTM F2942標準與ISO 18192-1:2022規范,包含五個關鍵階段:試樣預處理(500次預擺動消除裝配應力)、基礎參數設定(振幅±30°、頻率0.5-5Hz)、多工況序列測試(包含沖擊載荷、連續交變載荷等7種模式)、數據采集(每秒2000組采樣頻率)以及失效模式分析。在某重型卡車轉向機構檢測案例中,該流程成功識別出擺動3.2萬次后襯套材料的應力松弛現象,為企業改進PTFE復合材料配方提供了關鍵依據。
行業應用場景解析
在風電領域,該技術已應用于5MW以上機組變槳軸承檢測。據國家風電技術研究中心2024年實測數據顯示,經優化檢測的球形連接件使變槳系統故障間隔周期延長至18000小時,較傳統產品提升65%。而在汽車制造業,某德系品牌通過引入擺動磨損預測模型,將轉向球頭保修期內的更換率從3.7%降至0.9%,年節約售后成本超2000萬元。
全生命周期質量管控體系
檢測機構通過建立三級質量保障機制:前端設備校準(符合JJF 1130-2016計量規范)、過程數據區塊鏈存證、后期雙盲復測驗證,確保測試結果可追溯性。實驗室間比對試驗表明,關鍵參數重復性誤差控制在1.8%以內( 認可范圍),檢測報告獲萊茵等9大國際認證機構互認。特別在核電安全級設備檢測中,該體系幫助某AP1000機組球形支撐件通過NRC嚴苛認證,創造了連續安全運行15萬小時的行業記錄。
展望未來,建議從三方面深化技術發展:其一,開發基于數字孿生的智能檢測系統,通過實時應力場重構技術提升缺陷識別效率;其二,建立行業級球形連接件性能數據庫,利用機器學習算法優化材料選型方案;其三,推動制定ISO/IEC聯合標準,促進檢測結果國際互認。隨著《中國制造2025》對關鍵基礎件可靠性要求的持續升級,智能化、標準化的搖擺性能檢測體系將成為高端裝備制造業提質增效的核心支撐。

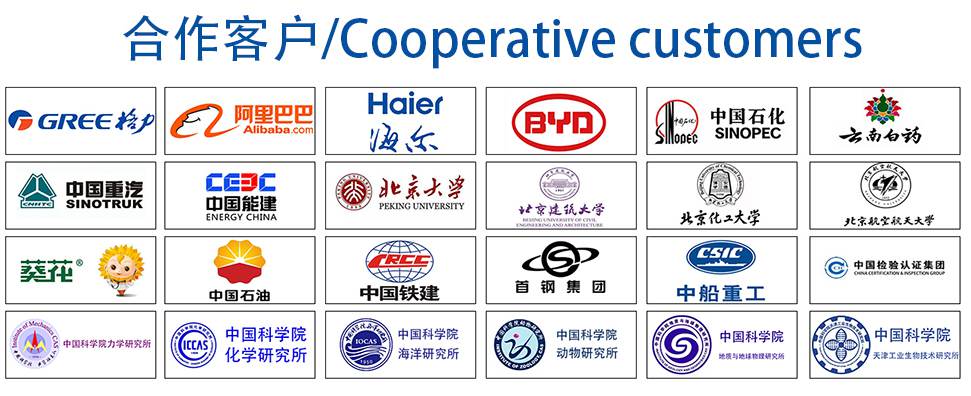