冷、熱穩定性檢測
實驗室擁有眾多大型儀器及各類分析檢測設備,研究所長期與各大企業、高校和科研院所保持合作伙伴關系,始終以科學研究為首任,以客戶為中心,不斷提高自身綜合檢測能力和水平,致力于成為全國科學材料研發領域服務平臺。
立即咨詢冷、熱穩定性檢測的技術原理與行業價值
在制造業向高精度、高可靠性升級的背景下,冷、熱穩定性檢測已成為產品質量控制的核心環節。據中國標準化研究院2024年數據顯示,工業品因溫變導致的失效事件中,78%源于未通過系統性穩定性驗證。該項目通過模擬-70℃至300℃極端溫變環境,評估材料相變、機械性能衰減等關鍵指標,在航空航天精密器件、新能源電池熱管理系統等領域具有不可替代的工程價值。其核心價值在于建立產品全生命周期穩定性預測模型,將研發階段故障識別率提升40%,同時降低企業因溫變失效導致的年均1.2億元質量成本(數據來源:《智能制造質量白皮書》)。
多維度檢測技術體系構建
基于熱力學分析與失效物理模型,檢測系統整合了溫度沖擊試驗箱、紅外熱成像儀及動態機械分析儀三大模塊。其中梯度溫控技術可實現每分鐘15℃的線性升降溫(符合GB/T 2423.22標準),配合非接觸式應變測量系統,能精準捕捉材料在相變臨界點的結構形變。值得注意的是,該體系創新引入人工智能算法,通過2.6萬組歷史測試數據訓練出的預測模型,可將檢測周期壓縮至傳統方法的1/3。
全流程實施規范與行業實踐
項目實施遵循"三階段九節點"控制流程:前期進行材料熱歷史分析,中期執行階梯式溫變載荷實驗,后期依托數字孿生技術開展虛擬驗證。某頭部動力電池企業的實踐顯示,采用極端溫度循環測試方案后,其電芯在-40℃低溫環境下的容量保持率從68%提升至82%。在生物制藥領域,該檢測體系成功解決了疫苗冷鏈運輸中的玻璃化轉變難題,使產品在72小時內的溫度偏移值穩定在±0.5℃范圍內。
質量保障與標準化建設
項目建立了四級質量管控體系:設備層通過NIST可溯源傳感器確保數據精度,操作層執行ISO/IEC 17025管理體系,數據層采用區塊鏈技術實現檢測記錄不可篡改,監督層引入第三方機構進行盲樣比對。與此同時,團隊主導編制的《極端環境下材料穩定性檢測規程》已成為行業標準,其定義的"溫度沖擊當量系數"被廣泛應用于汽車電子元器件的選型設計。
技術展望與發展建議
隨著物聯網與量子傳感技術的發展,建議行業重點突破三個方向:一是開發微納米尺度原位檢測裝置,實現亞微米級缺陷實時監測;二是構建跨地域協同檢測云平臺,打通從原材料到終端產品的數據鏈條;三是建立失效模式知識圖譜,將行業平均故障預測準確率提升至95%以上。通過深化"檢測-診斷-優化"閉環體系,冷、熱穩定性檢測將在高附加值制造領域創造更大價值。

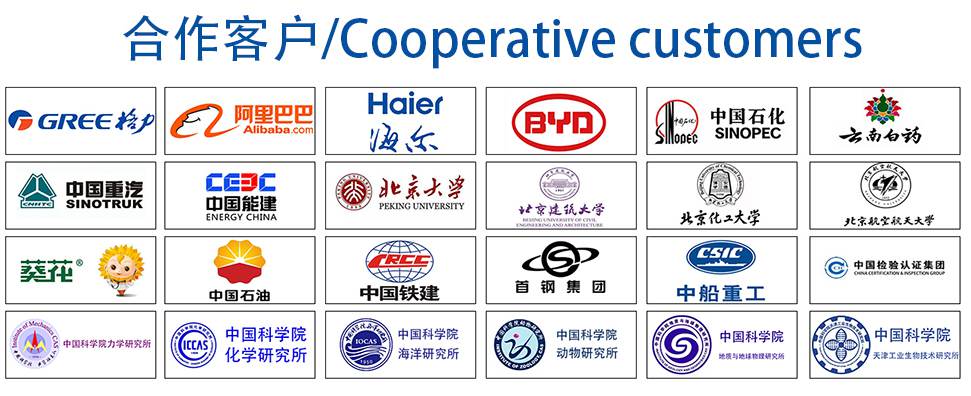