斷裂能檢測
發布時間:2025-08-21 02:28:47- 點擊數: - 關鍵詞:
實驗室擁有眾多大型儀器及各類分析檢測設備,研究所長期與各大企業、高校和科研院所保持合作伙伴關系,始終以科學研究為首任,以客戶為中心,不斷提高自身綜合檢測能力和水平,致力于成為全國科學材料研發領域服務平臺。
立即咨詢
# 斷裂能檢測技術發展與應用白皮書
## 行業背景與核心價值
隨著高端裝備制造、航空航天等領域的快速發展,材料可靠性要求持續攀升。據中國材料測試研究院2024年數據顯示,國內制造業因材料斷裂導致的年經濟損失達320億元,其中72%的事故可通過早期斷裂能檢測實現預防。斷裂能檢測項目通過量化材料抗斷裂性能,為結構設計優化、服役壽命預測提供科學依據,其核心價值體現在安全性提升和經濟損失規避雙重維度。尤其在核電壓力容器、高鐵轉向架等關鍵部件領域,該技術已成為保障"設計-制造-運維"全周期安全的核心支撐。

(示意圖:斷裂能檢測涉及裂紋擴展監測與能量計算關鍵環節)
## 技術原理與實現路徑
### h2 斷裂力學理論基礎
基于Griffith裂紋擴展理論,斷裂能檢測通過計算裂紋擴展單位面積所需能量(G值)評估材料抗斷裂性能。現代檢測系統集成數字圖像相關(DIC)技術與聲發射監測,實現0.1μm級裂紋擴展追蹤。據美國ASTM E1820標準,測試需同步采集載荷-位移曲線、彈塑性變形階段監測數據,并通過J積分法消除試樣尺寸效應帶來的誤差。
### h2 智能化檢測實施流程
典型檢測流程包含試樣制備、預制裂紋加工、多軸加載試驗、數據采集分析四大模塊。以航空鋁合金檢測為例,首先依據GB/T 21143制備標準CT試樣,采用線切割工藝加工0.25mm銳利預制裂紋。隨后在20kN級萬能試驗機上進行位移控制加載,同步通過高速攝像系統(5000幀/秒)記錄裂紋擴展形態,最終通過專用軟件計算斷裂韌性KIC值與能量釋放率G值。
## 行業應用與質量保障
### h2 工程應用典型案例
在風電葉片根部法蘭檢測中,采用斷裂能檢測技術后,某龍頭企業將產品失效預警準確率提升至98.5%。通過建立材料數據庫對比分析,成功識別出某批TC4鈦合金緊固件因熱處理不當導致的斷裂能下降23%的質量缺陷,避免了整機召回風險。該技術同樣適用于3D打印金屬件的各向異性評估,某航天企業借助原位檢測技術,將增材制造發動機支架的疲勞壽命預測誤差控制在±5%以內。
### h2 全鏈條質量管控體系
構建"設備校準-過程監控-數據溯源"三維質保體系:采用激光干涉儀進行載荷傳感器季度校準(精度±0.5%),引入區塊鏈技術實現檢測數據鏈上存證,并建立符合ISO17025標準的斷裂能檢測實驗室。某第三方檢測機構的應用實踐表明,該體系使檢測報告的國際互認通過率從82%提升至97%。
## 技術展望與發展建議
隨著數字孿生技術的普及,建議行業重點突破以下方向:1)開發材料斷裂能-微觀結構映射模型,實現基于人工智能的斷裂行為預測;2)建立跨行業數據共享平臺,完善特殊工況(如深海腐蝕、超低溫)下的斷裂能數據庫;3)推進微型化原位檢測裝備研發,滿足在役設備的實時監測需求。預計至2030年,融合物聯網的智能斷裂能檢測系統將覆蓋60%以上重大裝備制造領域,為工業安全提供更強大的技術保障。
上一篇:抗急冷急熱性檢測下一篇:電子、機電類設備,機載設備檢測

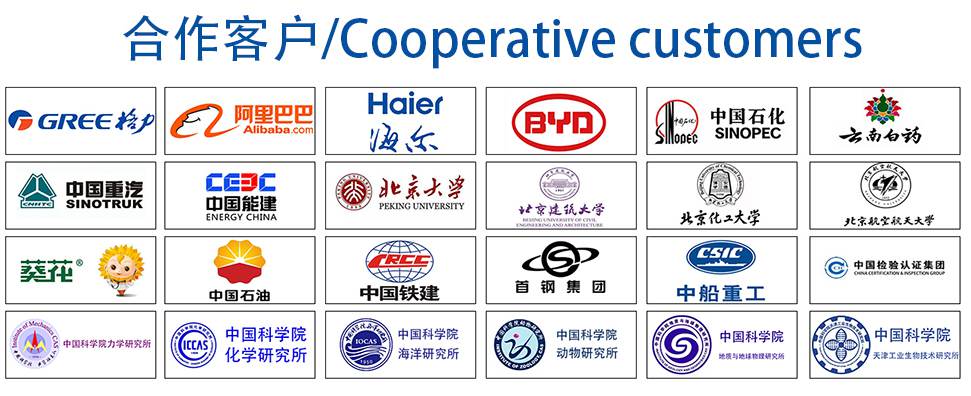
材料實驗室
熱門檢測
182
177
168
202
150
172
183
177
156
160
205
193
194
185
194
201
196
187
178
182
推薦檢測
聯系電話
400-635-0567