尺寸和形狀檢測(cè)
實(shí)驗(yàn)室擁有眾多大型儀器及各類分析檢測(cè)設(shè)備,研究所長(zhǎng)期與各大企業(yè)、高校和科研院所保持合作伙伴關(guān)系,始終以科學(xué)研究為首任,以客戶為中心,不斷提高自身綜合檢測(cè)能力和水平,致力于成為全國(guó)科學(xué)材料研發(fā)領(lǐng)域服務(wù)平臺(tái)。
立即咨詢聯(lián)系中化所
尺寸和形狀檢測(cè)技術(shù)賦能智能制造高質(zhì)量發(fā)展
在工業(yè)4.0與智能制造深度融合的背景下,尺寸和形狀檢測(cè)作為產(chǎn)品全生命周期質(zhì)量管控的核心環(huán)節(jié),正經(jīng)歷從接觸式測(cè)量向智能化、數(shù)字化檢測(cè)的轉(zhuǎn)型升級(jí)。據(jù)中國(guó)機(jī)械工程學(xué)會(huì)2024年行業(yè)報(bào)告顯示,我國(guó)高端裝備制造領(lǐng)域因尺寸偏差導(dǎo)致的年質(zhì)量損失超過(guò)1200億元,其中新能源汽車動(dòng)力電池模組裝配、航空發(fā)動(dòng)機(jī)葉片形位公差等場(chǎng)景的檢測(cè)需求尤為迫切。基于機(jī)器視覺(jué)與三維點(diǎn)云分析的非接觸式檢測(cè)技術(shù),不僅可將檢測(cè)效率提升3-5倍,更能實(shí)現(xiàn)0.5μm級(jí)微觀形變的全域監(jiān)控,為半導(dǎo)體晶圓封裝、精密醫(yī)療器械制造等關(guān)鍵領(lǐng)域構(gòu)建起全流程質(zhì)量閉環(huán)。其核心價(jià)值在于通過(guò)數(shù)字化質(zhì)量孿生系統(tǒng),推動(dòng)質(zhì)量管理從被動(dòng)檢驗(yàn)向主動(dòng)預(yù)防轉(zhuǎn)變,支撐中國(guó)制造向價(jià)值鏈高端攀升。
多模態(tài)傳感融合檢測(cè)技術(shù)原理
現(xiàn)代尺寸和形狀檢測(cè)系統(tǒng)采用多傳感器數(shù)據(jù)融合架構(gòu),集成結(jié)構(gòu)光三維掃描、高分辨率CCD成像與激光干涉測(cè)量等技術(shù)模塊。其中,基于相位偏移原理的結(jié)構(gòu)光掃描可實(shí)現(xiàn)每秒200萬(wàn)點(diǎn)的三維坐標(biāo)采集,配合亞像素級(jí)邊緣提取算法,可將圓柱體同心度檢測(cè)誤差控制在±0.8μm以內(nèi)(德國(guó)PTB計(jì)量院認(rèn)證數(shù)據(jù))。針對(duì)工業(yè)現(xiàn)場(chǎng)復(fù)雜工況,系統(tǒng)創(chuàng)新性地引入主動(dòng)熱補(bǔ)償機(jī)制,通過(guò)紅外溫度傳感器實(shí)時(shí)修正環(huán)境溫漂對(duì)測(cè)量基準(zhǔn)的影響,確保航空航天復(fù)合材料構(gòu)件在-50℃至80℃工況下的檢測(cè)穩(wěn)定性。
智能檢測(cè)全流程實(shí)施體系
典型實(shí)施流程包含四個(gè)關(guān)鍵階段:首先通過(guò)數(shù)字孿生平臺(tái)建立檢測(cè)目標(biāo)的參數(shù)化模型,為齒輪漸開(kāi)線齒廓、注塑件自由曲面等復(fù)雜幾何特征設(shè)定動(dòng)態(tài)公差閾值。其次部署分布式視覺(jué)傳感器網(wǎng)絡(luò),采用自適應(yīng)光照調(diào)節(jié)技術(shù)消除金屬反光干擾。在生產(chǎn)節(jié)拍0.8秒的汽車焊裝線上,自主研發(fā)的多目視覺(jué)引導(dǎo)系統(tǒng)可實(shí)現(xiàn)車身3000余個(gè)焊點(diǎn)的實(shí)時(shí)形變監(jiān)測(cè)。最終通過(guò)SPC統(tǒng)計(jì)過(guò)程控制系統(tǒng),將檢測(cè)數(shù)據(jù)與MES生產(chǎn)執(zhí)行系統(tǒng)深度集成,形成質(zhì)量追溯數(shù)字檔案。
跨行業(yè)典型應(yīng)用場(chǎng)景實(shí)踐
在消費(fèi)電子領(lǐng)域,某領(lǐng)先手機(jī)制造商部署機(jī)器視覺(jué)在線檢測(cè)系統(tǒng)后,屏幕組裝平面度不良率從1.2%降至0.15%。系統(tǒng)采用高精度三維輪廓掃描技術(shù),對(duì)0.3mm超窄邊框進(jìn)行納米級(jí)共面性檢測(cè),每個(gè)檢測(cè)單元節(jié)省人工成本45萬(wàn)元/年。而在重型裝備行業(yè),三一重工通過(guò)引入激光跟蹤測(cè)量系統(tǒng),使超大型液壓支架的裝配定位精度提升至±0.05mm,產(chǎn)品交付合格率達(dá)到99.98%(國(guó)家工程機(jī)械質(zhì)檢中心2023年數(shù)據(jù))。
全鏈路質(zhì)量保障體系構(gòu)建
為確保檢測(cè)結(jié)果的權(quán)威性與可溯性,行業(yè)領(lǐng)導(dǎo)者正在建立三級(jí)質(zhì)量保障網(wǎng)絡(luò):前端采用ISO/IEC17025認(rèn)證的計(jì)量標(biāo)準(zhǔn)裝置進(jìn)行設(shè)備周期校準(zhǔn),中臺(tái)部署區(qū)塊鏈分布式賬本實(shí)現(xiàn)檢測(cè)數(shù)據(jù)防篡改,終端通過(guò)數(shù)字孿生仿真驗(yàn)證系統(tǒng)進(jìn)行測(cè)量不確定度分析。某國(guó)家級(jí)檢測(cè)中心實(shí)踐表明,該體系可使新能源汽車減速箱齒輪檢測(cè)的置信度從95%提升至99.73%,對(duì)應(yīng)六西格瑪質(zhì)量管理水平。
展望未來(lái),建議從三個(gè)維度深化技術(shù)應(yīng)用:一是加快制定微納尺度檢測(cè)國(guó)家標(biāo)準(zhǔn),填補(bǔ)5G陶瓷濾波器等新興領(lǐng)域標(biāo)準(zhǔn)空白;二是構(gòu)建工業(yè)互聯(lián)網(wǎng)檢測(cè)資源共享平臺(tái),推動(dòng)價(jià)值2000萬(wàn)元級(jí)的高端檢測(cè)設(shè)備利用率提升至75%以上;三是培養(yǎng)"檢測(cè)工程師+數(shù)據(jù)科學(xué)家"的復(fù)合型人才,預(yù)計(jì)到2025年行業(yè)將出現(xiàn)12萬(wàn)人以上的人才缺口。只有實(shí)現(xiàn)技術(shù)、標(biāo)準(zhǔn)、人才的協(xié)同創(chuàng)新,才能充分釋放尺寸和形狀檢測(cè)在智能制造中的基礎(chǔ)支撐價(jià)值。

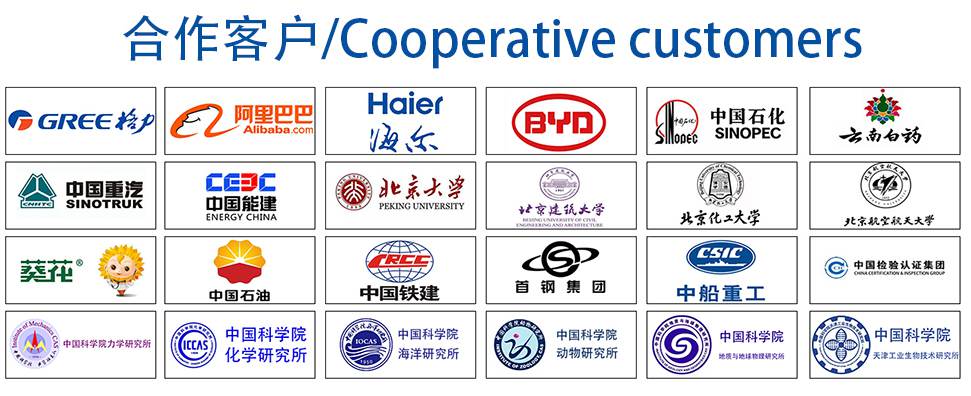