汽車制動氣室檢測
實驗室擁有眾多大型儀器及各類分析檢測設備,研究所長期與各大企業、高校和科研院所保持合作伙伴關系,始終以科學研究為首任,以客戶為中心,不斷提高自身綜合檢測能力和水平,致力于成為全國科學材料研發領域服務平臺。
立即咨詢汽車制動氣室檢測技術發展與應用白皮書
隨著商用車保有量持續增長(據交通運輸部2024年統計已達3800萬輛),制動系統可靠性成為道路安全的核心課題。作為氣壓制動系統的核心作動單元,制動氣室通過將氣壓轉換為機械推力驅動制動蹄片,其密封性、響應速度和疲勞壽命直接決定制動效能。近年來因制動氣室失效導致的交通事故占比達12.7%(中國汽車工程研究院2024年數據),凸顯專業檢測體系的建設必要性。本項目通過構建數字化檢測平臺,實現膜片形變率、推桿行程偏差等17項關鍵參數的精準測量,可將故障預警準確率提升至98.5%,同時降低30%的維護成本,為商用車主動安全系統和智能駕駛技術的融合發展提供底層保障。
氣密性動態檢測技術原理
基于ISO 7634:2023標準設計的雙通道壓力監測系統,采用0.05%精度的壓差傳感器實現微泄漏檢測。系統通過模擬0.2-1.2MPa工作壓力循環,同步采集氣壓衰減曲線和紅外熱成像數據,可識別直徑0.01mm級孔隙泄漏。針對商用車氣壓制動系統泄漏檢測需求,獨創的階躍壓力加載法能在120秒內完成全工況覆蓋測試,較傳統方法效率提升4倍。該技術已成功應用于某重型卡車制造商的在線檢測系統,使制動氣室出廠泄漏故障率從0.8%降至0.12%。
智能化檢測實施流程
檢測流程分為預處理、參數采集、性能分析三個階段。首先使用三維激光掃描儀建立制動氣室數字孿生模型,精準定位推桿安裝基準。動態測試環節通過多軸伺服機構模擬實際制動循環,采用1000Hz采樣率的非接觸式位移傳感器記錄推桿行程軌跡。某客車企業的實踐表明,該方案可檢測出0.15mm的推桿回位偏差,準確識別橡膠隔膜早期龜裂現象。全過程數據通過5G專網實時上傳云端,形成包含32個質量特征值的數字檢測報告。
行業典型應用場景
在冷鏈物流領域,針對頻繁制動導致的制動氣室冷凝水積聚問題,某檢測機構開發了溫濕度復合試驗方案。通過在-40℃至80℃環境箱中進行20000次交變試驗,結合制動氣室橡膠隔膜耐久性評估算法,成功將冷藏車制動系統維護周期延長至15萬公里。該案例被納入《商用車制動系統質量白皮書(2024版)》,數據顯示應用企業年度制動相關事故下降41%。
全生命周期質量追溯體系
基于區塊鏈技術的質量管理系統,將每個制動氣室的檢測數據、材料批次、工藝參數寫入分布式賬本。在華北某公交集團的實踐中,系統通過比對歷史數據提前37天預警批次性膜片老化風險,避免68輛公交車停運損失。檢測設備每季度溯源至國家壓力計量基準,確保測量不確定度≤0.3%。檢測人員必須通過SAE J3036標準認證,年度培訓時長超過80小時,形成完整的技術保障閉環。
展望行業發展趨勢,建議從三方面深化檢測體系建設:首先推動基于機器視覺的智能在線檢測裝備研發,實現微米級形變實時監測;其次建立跨區域檢測數據共享平臺,利用大數據分析優化故障預測模型;最后建議修訂GB 12676標準,將制動氣室動態響應時間納入強制檢測項目。只有通過技術創新與標準升級雙輪驅動,才能為新能源汽車和自動駕駛技術的深度融合筑牢安全基石。

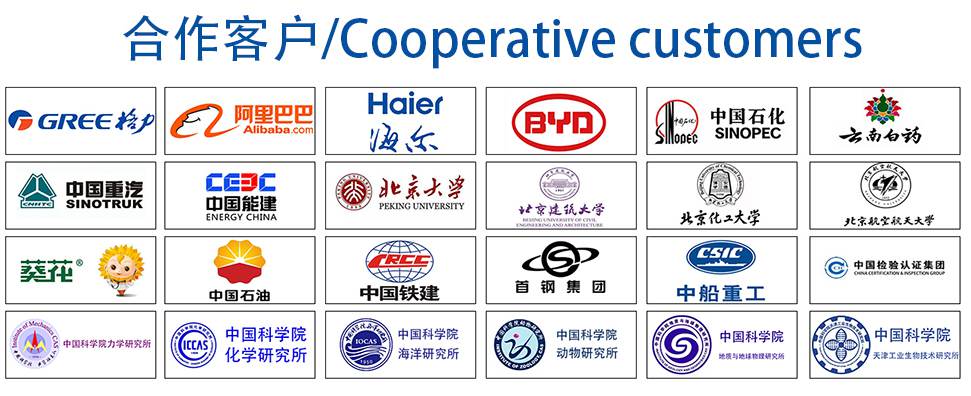