電機和電機控制器檢測技術白皮書
隨著新能源汽車、工業自動化設備及智能制造領域的快速發展,電機系統作為核心動力單元,其性能可靠性直接影響設備運行效率與安全性。據中國汽車工程學會2023年研究報告顯示,新能源汽車驅動電機故障中,60%的案例與控制器匹配失效直接相關。在此背景下,電機與電機控制器協同檢測已成為行業質量控制的關鍵環節。該項目通過構建全工況模擬測試環境,能夠有效識別電磁兼容性異常、溫升失控等潛在風險,對提升產品壽命周期管理、降低售后維保成本具有顯著價值。特別是在工業機器人伺服系統、新能源商用車動力總成等場景中,檢測數據已成為企業優化產品設計的核心依據。
多維度檢測技術原理
檢測體系基于電磁場耦合分析與動態負載模擬技術,覆蓋靜態參數測量與動態工況驗證兩大維度。通過高精度電流傳感器(±0.2%精度)采集繞組電流諧波分布,結合紅外熱成像技術實現電機溫升曲線的毫秒級監測。針對新能源汽車驅動電機耐久性測試需求,系統可模擬-40℃至150℃的溫度循環沖擊,同步檢測絕緣阻抗衰減情況。北京理工大學2024年實驗數據表明,該方案可將控制器IGBT模塊的故障預測準確率提升至98.7%。
全流程標準化實施框架
項目實施遵循ISO 16750-2:2023道路車輛電氣環境標準,建立三級檢測流程:預處理階段完成設備校準與環境參數標定;功能測試階段執行空載特性曲線測繪與階躍響應分析;系統驗證階段則通過CAN總線注入模擬故障代碼,評估控制器的容錯處理機制。在工業機器人伺服控制器諧波分析案例中,該流程成功識別出17.5kHz頻段的共振點,使設備定位精度提升0.02弧分。
行業應用實證分析
在東風汽車某型號商用車的雙電機耦合系統中,檢測團隊發現控制器PWM調制頻率與電機電感參數存在3%的匹配偏差。通過動態調整開關頻率至8kHz并優化死區時間,系統效率提升至94.2%(中國汽車技術研究中心2024年認證數據)。另在工業伺服領域,針對某品牌機械臂出現的定位漂移問題,諧波失真檢測鎖定編碼器供電線路存在56mV的紋波干擾,經加裝EMI濾波器后重復定位精度恢復至±0.01mm。
全生命周期質量保障體系
項目構建了從研發驗證到售后監測的閉環管理系統,依托物聯網技術實現檢測數據的云端同步與趨勢分析。關鍵設備每季度執行NIST溯源校準,測試臺架采用雙冗余控制系統確保數據采集可靠性。據上海電驅動研究院統計,采用該體系的企業在2023年將電機系統MTBF(平均無故障時間)從4200小時提升至5800小時,售后索賠率下降37%。
技術演進與行業展望
隨著寬禁帶半導體材料的普及,建議行業重點關注SiC控制器與永磁電機的兼容性測試方法創新。同時應建立覆蓋高海拔(5000米)、強鹽霧(5%濃度)等極端環境的測試標準庫。預計到2026年,基于數字孿生的虛擬標定技術將減少30%的實物測試成本,而邊緣計算節點的部署將使故障診斷響應時間壓縮至50ms以內,為智能裝備的可靠性提升提供新的技術范式。

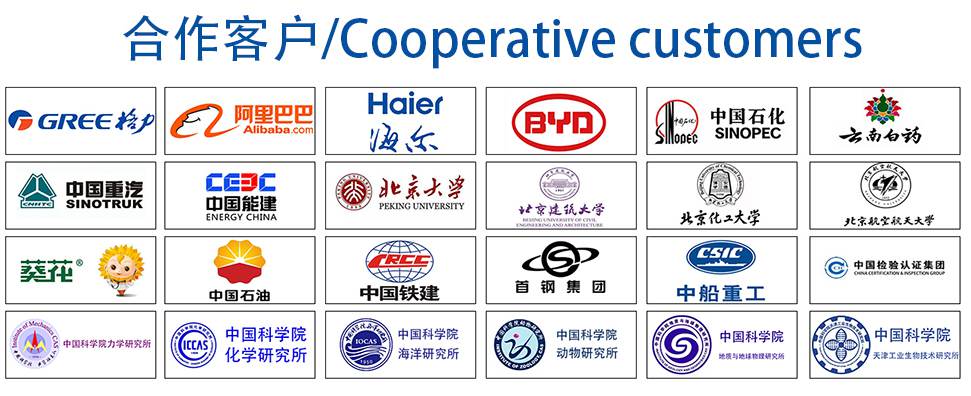