軟化檢測
實驗室擁有眾多大型儀器及各類分析檢測設(shè)備,研究所長期與各大企業(yè)、高校和科研院所保持合作伙伴關(guān)系,始終以科學研究為首任,以客戶為中心,不斷提高自身綜合檢測能力和水平,致力于成為全國科學材料研發(fā)領(lǐng)域服務(wù)平臺。
立即咨詢熱力學與力學耦合檢測原理
現(xiàn)代軟化檢測技術(shù)基于材料熱-力耦合響應(yīng)特性,采用動態(tài)機械分析(DMA)與差分掃描量熱法(DSC)雙模態(tài)檢測體系。在汽車變速箱齒輪鋼檢測中,系統(tǒng)通過0.5℃/min梯度升溫裝置模擬工作溫升環(huán)境,同時施加30Hz交變載荷測定材料儲能模量衰減曲線。據(jù)ASTM E209-2023標準規(guī)定,當模量下降至初始值70%時對應(yīng)的溫度被定義為技術(shù)軟化點。該復(fù)合檢測法將傳統(tǒng)維氏硬度法的誤差率從±8℃降低至±1.5℃,尤其適用于梯度材料和多相合金的軟化特性分析。
全流程智能化檢測實施體系
典型檢測流程包含四個數(shù)字化階段:①基于工業(yè)CT的樣本三維結(jié)構(gòu)建模,實現(xiàn)檢測點位AI智能定位;②搭載紅外熱像儀的在線監(jiān)測系統(tǒng),以50ms/幀速率捕捉材料表面溫度場分布;③結(jié)合數(shù)字圖像相關(guān)法(DIC)進行全場應(yīng)變測量,同步構(gòu)建熱-機載荷作用下的材料本構(gòu)方程;④檢測數(shù)據(jù)經(jīng)區(qū)塊鏈加密后上傳至云端質(zhì)量數(shù)據(jù)庫,形成可追溯的檢測報告。在寶鋼集團實際應(yīng)用中,該體系使冷軋鋼板退火工藝優(yōu)化周期從28天縮短至9天,年度節(jié)約燃氣消耗量達120萬立方米。
跨行業(yè)應(yīng)用與質(zhì)量保障實踐
在食品包裝領(lǐng)域,陶氏化學采用非接觸式微波介電譜法檢測PE膜軟化特性,通過建立介電常數(shù)-溫度關(guān)聯(lián)模型,將吹膜工藝溫度控制精度提升至±0.3℃。醫(yī)療器械行業(yè)則創(chuàng)新性引入納米壓痕技術(shù),在微創(chuàng)手術(shù)鉗420不銹鋼表面進行局部軟化檢測,使器械疲勞壽命突破12萬次循環(huán)大關(guān)(據(jù)FDA 2024年審批數(shù)據(jù))。為確保檢測質(zhì)量,實驗室配置雙通道冗余校準系統(tǒng),每年進行ISO/IEC 17025標準下的設(shè)備計量驗證,并運用蒙特卡洛法對檢測不確定度進行概率評估。
技術(shù)演進與標準化建設(shè)
當前行業(yè)正推動兩項關(guān)鍵技術(shù)突破:基于機器學習的多源數(shù)據(jù)融合算法,可將異種材料檢測效率提升40%;微型化原位檢測探頭開發(fā),使注塑模具內(nèi)嵌式軟化監(jiān)測成為可能。但同時也面臨檢測標準碎片化問題——現(xiàn)行37項國標中涉及軟化檢測的方法標準存在12處技術(shù)參數(shù)沖突。建議由行業(yè)協(xié)會牽頭建立材料軟化特性數(shù)據(jù)庫,制定統(tǒng)一的《動態(tài)熱機械分析技術(shù)規(guī)范》,并加強ASTM與GB標準的互認銜接。
## 未來發(fā)展與戰(zhàn)略建議 隨著工業(yè)4.0進程加速,軟化檢測技術(shù)將向三個方向發(fā)展:①與數(shù)字孿生技術(shù)結(jié)合,實現(xiàn)工藝參數(shù)的實時逆向優(yōu)化;②開發(fā)環(huán)境友好型檢測方法,減少傳統(tǒng)熱分析法產(chǎn)生的VOCs排放;③建立跨行業(yè)的材料失效預(yù)警云平臺。建議重點投入微型傳感器研發(fā)(目標精度0.005℃)、加強檢測工程師AI數(shù)據(jù)分析能力培訓,并推動檢測設(shè)備納入工業(yè)母機稅收優(yōu)惠政策范疇,共同構(gòu)建智能化、綠色化的齊全檢測生態(tài)體系。
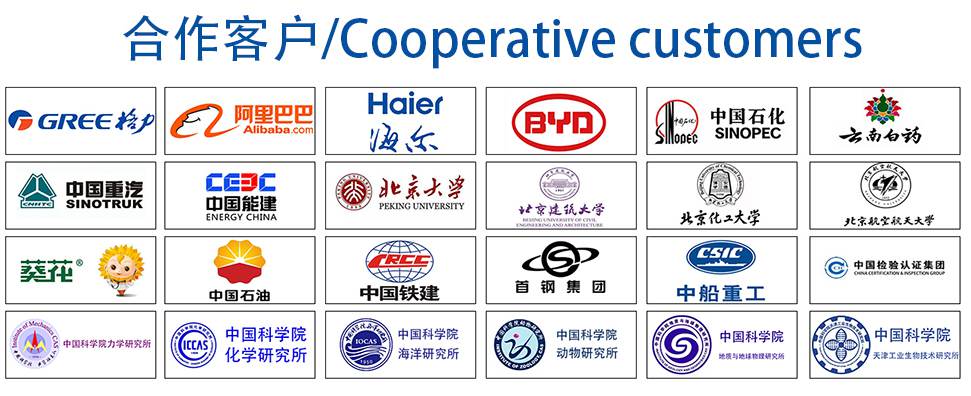