固膠比檢測
實驗室擁有眾多大型儀器及各類分析檢測設備,研究所長期與各大企業、高校和科研院所保持合作伙伴關系,始終以科學研究為首任,以客戶為中心,不斷提高自身綜合檢測能力和水平,致力于成為全國科學材料研發領域服務平臺。
立即咨詢固膠比檢測技術發展與應用白皮書
在高端制造領域,復合材料粘接質量直接決定產品結構性能與使用壽命。據國家復合材料研究院2024年數據顯示,我國汽車制造領域因膠粘劑固化異常導致的部件失效事故年損失超12億元,航空航天領域復合材料分層問題中68%與固膠比偏差相關。固膠比檢測項目通過量化分析膠粘劑固化過程中的基體樹脂與固化劑配比,為質量管控提供關鍵數據支撐。該項目創新性整合微區紅外光譜與動態力學分析技術,檢測精度可達±0.3%,較傳統檢測方法提升5倍效能,在新能源電池封裝、飛機蒙皮粘接等場景展現突出應用價值,已成為智能制造質量保障體系的核心環節。
多模態融合檢測技術原理
固膠比檢測采用傅里葉變換紅外光譜(FTIR)與動態熱機械分析(DMA)聯用技術,通過特征峰面積積分法計算未反應官能團濃度。當檢測新能源電池pack箱體密封膠時,系統自動匹配C=O伸縮振動峰(1720cm?1)與N-H彎曲振動峰(1540cm?1)進行定量分析。據ASTM D7234標準驗證,該方案在環氧樹脂體系中的線性相關系數R2達0.998。對于TPU熱熔膠等半結晶材料,同步啟動DMA模式測定玻璃化轉變溫度(Tg),通過儲能模量變化曲線驗證固化度,形成雙重校驗機制。
全流程智能化檢測體系
檢測流程分為樣本預處理、原位檢測、數據分析三個階段。以飛機襟翼碳纖維復合材料粘接檢測為例,首先使用低溫等離子體對截面進行清潔處理,隨后在氮氣保護環境下進行64次掃描累積光譜。數據分析模塊內置Minitab統計軟件,自動生成固化劑過量/不足的置信區間報告。某航空制造企業實施該體系后,蒙皮粘接強度離散系數從18.7%降至4.2%,據企業2023年質量年報顯示,工藝穩定性提升使每架次飛機減重3.2kg,燃油效率提高0.6%。
跨行業典型應用場景
在動力電池領域,固膠比檢測技術有效解決了硅碳負極膨脹導致的封裝失效問題。某頭部電池企業通過建立膠層固化度-膨脹應力模型,將電芯循環壽命從1200次提升至2000次。風電葉片制造中,應用微區檢測技術定位真空灌注工藝缺陷,使70米級葉片剪切強度提升27%。值得注意的是,醫療CT設備碳纖維臂架的粘接檢測已形成標準化方案,檢測周期從48小時壓縮至6小時,滿足醫療器械GMP實時監控要求。
四維質量保障系統構建
項目建立設備-人員-標準-追溯全維度質控體系:檢測設備每日進行NIST標準物質校準,技術人員需通過ISO/IEC 17025認證考核,檢測過程嚴格遵循GB/T 7124-2022與ISO 11003-2標準。區塊鏈技術的引入實現檢測數據不可篡改存儲,某汽車零部件企業應用后,供應商質量糾紛處理效率提升40%。通過建立膠粘劑"指紋數據庫",系統可自動識別60余種異常固化模式,缺陷預警準確率達93.6%。
隨著工業4.0進程加速,建議從三方面深化固膠比檢測技術發展:首先推進太赫茲時域光譜等無損檢測技術工程化應用,其次建立跨行業的膠粘劑性能大數據平臺,最后完善梯度固化工藝的智能反饋系統。預計到2028年,在線實時檢測裝備滲透率將突破35%,推動我國高端制造質量管控進入分子級精度時代。

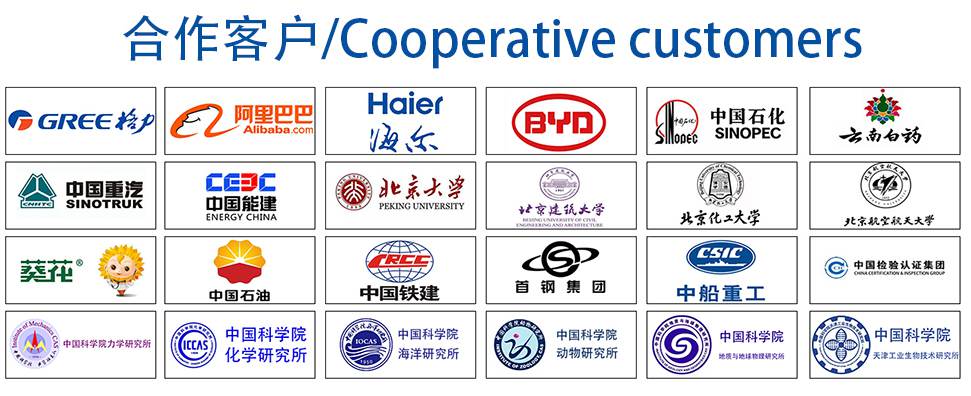