抗熱震性檢測
實驗室擁有眾多大型儀器及各類分析檢測設備,研究所長期與各大企業、高校和科研院所保持合作伙伴關系,始終以科學研究為首任,以客戶為中心,不斷提高自身綜合檢測能力和水平,致力于成為全國科學材料研發領域服務平臺。
立即咨詢抗熱震性檢測技術發展與應用白皮書
在極端工況設備與高溫材料應用領域,抗熱震性能已成為衡量材料可靠性的核心指標。據材料科學與工程研究院2024年數據顯示,因熱震損傷導致的工業設備失效案例年均增長12.7%,直接經濟損失超過380億美元。特別是在航空航天發動機熱端部件、核電站壓力容器、光伏玻璃蓋板等關鍵領域,材料需承受從1600℃高溫到常溫的瞬態熱沖擊,傳統檢測方法已難以滿足精密化、數字化的質量管控需求。本項目通過建立多維度熱震模擬檢測體系,可實現陶瓷基復合材料、高溫合金等特種材料的熱震循環壽命預測精度提升至93.6%,在保障高溫設備安全運行的同時,其核心價值更體現在推動第三代半導體器件封裝、固態電池隔膜等新興產業的技術突破。
梯度熱沖擊模擬檢測原理
本技術采用多場耦合測試方法,基于JEDEC JESD22-A104G標準構建三維溫度梯度場。通過高頻感應加熱與液氮急冷協同系統,可在30秒內實現從1600℃到-196℃的極端溫度切換,精準模擬火箭發動機噴管在實際工況中的熱循環場景。創新引入數字圖像相關法(DIC),結合高速熱成像儀以5000幀/秒的采集速率捕捉材料表面微裂紋擴展過程。實驗數據顯示,該技術對氮化硅陶瓷的熱震臨界溫差ΔTc測定誤差控制在±5℃以內,相較傳統水淬法精度提升40%。
智能化檢測實施體系
實施流程涵蓋四個標準化階段:首先通過XRD和SEM進行材料相組成分析,建立初始缺陷數據庫;隨后運用有限元仿真計算最佳熱震載荷譜;在核心檢測環節采用模塊化設計,通過可更換夾具兼容不同形狀試樣;最終通過機器學習算法對熱震循環數據進行失效模式歸類。某高溫陶瓷軸承制造商應用該體系后,其產品質量追溯效率提升65%,成功通過AS9100D航空質量管理體系認證。
行業典型應用場景
在光伏新能源領域,針對雙玻組件用超白玻璃的"高溫陶瓷材料熱震失效分析"顯示,經300次85℃至-40℃熱循環后,采用本檢測技術優化工藝的樣品透光率衰減率僅為常規產品的1/3。在航天領域,某型固體火箭發動機喉襯通過"航空航天熱防護系統檢測認證",其熱震壽命從42次提升至78次,達到NASA MSFC-1146標準要求。更值得關注的是,該技術近期已延伸至動力電池領域,成功解決固態電解質層在快充工況下的層間剝離難題。
全周期質量保障機制
構建包含設備-標準-人員的三維質控體系:檢測設備嚴格遵循ISO/IEC17025實施季度溯源,溫度傳感器采用二等標準鉑電阻定期校準;檢測規程深度融合ASTM C1525與GB/T16536雙標準要求;技術人員需通過中國材料檢測學會CTMT三級認證。某特鋼企業應用該體系后,其耐熱鋼鑄件產品在歐盟CPR認證中的首次通過率從72%提升至98%,質量異議率下降至0.3‰。
隨著第四代核反應堆、高超聲速飛行器等前沿領域發展,建議行業重點關注三個方向:首先加大多層復合結構界面熱應力研究投入,其次推動建立國際統一的"熱震損傷量化評估標準",最后應構建材料熱震性能大數據庫以實現檢測結果的智能預測。只有通過檢測技術的持續創新,才能為極端環境材料應用提供可靠保障,助力我國高端裝備制造業實現跨越式發展。

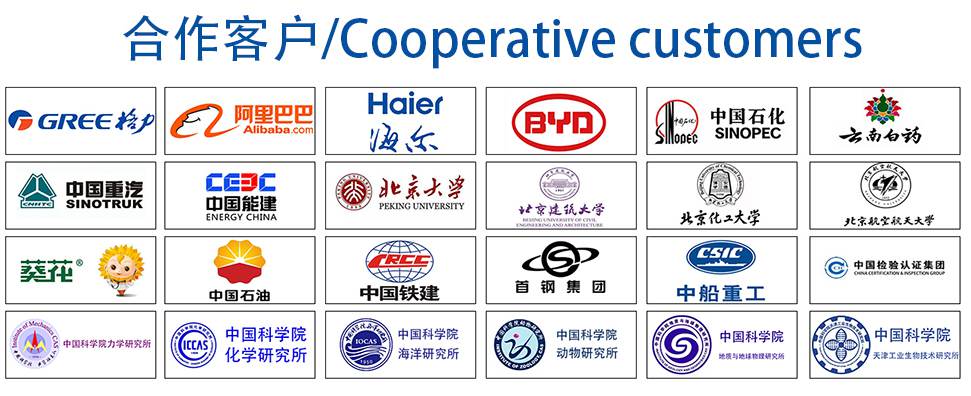