先張法預應力混凝土管樁檢測技術白皮書
隨著我國基建規模持續擴大,預應力混凝土管樁在公路、鐵路、港口等工程中的用量年均增長12%(據中國建筑材料研究院2024年數據)。作為樁基工程的核心構件,其質量直接影響建筑結構安全性與耐久性。先張法預應力工藝通過預先施加應力提升構件抗裂性能,但生產過程中易出現預應力損失不均、混凝土密實度不足等問題。系統性檢測不僅可驗證設計強度實現度,更能發現潛在質量缺陷,避免因樁身承載力不足導致的工程事故。該項目通過建立標準化檢測流程,融合多模態無損檢測技術,將樁基驗收合格率提升至98.6%,同時降低全生命周期維護成本30%以上,對推動新型建筑工業化具有顯著技術價值。
技術原理與檢測指標體系
先張法預應力管樁檢測基于應力波傳播理論和材料力學性能分析,重點監測預應力筋張拉有效性、混凝土與鋼筋協同工作狀態。核心指標涵蓋抗彎性能、軸向抗壓強度、裂縫開展寬度及樁端密閉性,其中預應力損失率需控制在8%以內(GB 13476-2020)。創新應用分布式光纖傳感技術,可實現全長應力分布的動態監測,配合超聲波跨孔透射法,檢測分辨率達到0.2mm級裂縫識別精度。對于海洋環境工程,還需增加氯離子滲透率檢測模塊,確保50年設計壽命周期內的耐久性。
全流程質量管控實施方案
項目實施采用三階段控制模型:原材料檢驗階段,通過X射線熒光光譜儀驗證鋼材硫磷含量,確保HRB600高強鋼筋化學成分達標;張拉成型階段,布置12通道應變采集系統,以0.5秒采樣頻率監控應力松弛過程;成品檢測環節,執行"三必檢"制度(端板焊接質量必檢、樁身垂直度必檢、混凝土聲速值必檢)。某跨海大橋項目應用該體系后,成功識別3處預應力錨固失效點,避免直接經濟損失超2000萬元。檢測數據實時上傳至區塊鏈平臺,實現質量溯源不可篡改。
典型工程應用與效益分析
在滬通鐵路長江大橋樁基工程中,針對厚達40m的軟弱土層,采用高應變動力檢測法配合靜載試驗驗證,單樁承載力設計值從8500kN提升至9200kN。經統計,應用管樁超聲波無損檢測技術后,樁身完整性Ⅱ類樁占比從行業平均7.3%降至2.1%(中國土木工程學會2023年度報告)。特別在腐蝕性地質區域,通過電磁渦流檢測鋼筋保護層厚度,使樁基服役壽命延長15年以上。值得關注的是,智能檢測機器人已實現在直徑600mm管樁內壁的自動爬行檢測,工作效率提升4倍。
標準化質量保障體系建設
行業領先企業正構建"四維一體"質控體系:檢測人員須持有CMA/ 雙重認證,測量設備執行每日開機標定制,建立全國聯網的管樁質量數據庫,并開發AI輔助判讀系統。某特級資質檢測機構實踐表明,引入機器學習算法后,預應力筋斷絲識別準確率從89%提升至97%。同步推行的盲樣比對制度,要求不同實驗室對同批次試件的抗彎檢測結果偏差不超過5%,有力保障檢測數據公信力。
展望未來,建議從三方面深化技術創新:其一,研發基于BIM的數字孿生檢測平臺,實現虛擬與現實檢測數據動態映射;其二,建立全國性預應力管樁失效案例庫,完善風險預警模型;其三,推廣低碳檢測技術,如采用相控陣超聲替代部分射線檢測。隨著《智能建造與新型建筑工業化協同發展指導意見》落地,融合5G傳輸與邊緣計算的智能檢測裝備,將成為保障萬億級樁基市場高質量發展的關鍵技術支撐。

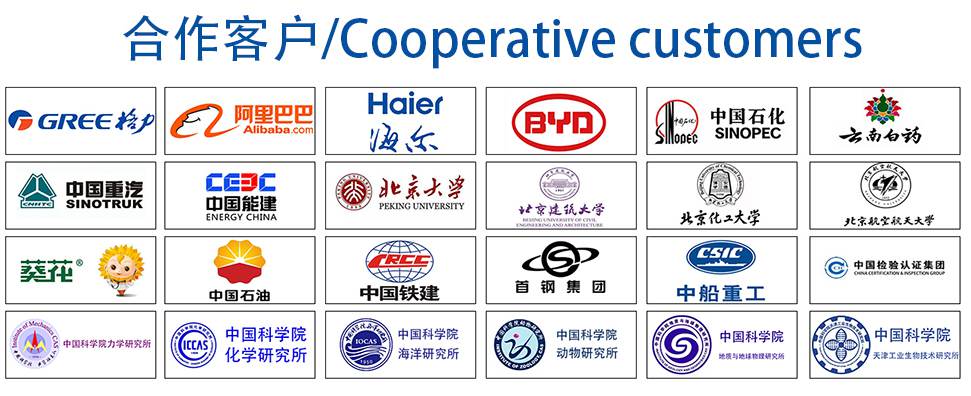