Y型球頭檢測技術白皮書
在汽車工業智能化轉型背景下,轉向系統核心零部件的質量控制已成為行業發展的關鍵環節。據中國汽車工業協會2024年數據顯示,我國汽車保有量突破3.8億輛,轉向系統故障在交通事故誘因中占比達12.7%。作為轉向機構的重要傳力部件,Y型球頭的幾何精度、材料強度和疲勞壽命直接影響車輛操縱穩定性與行駛安全性。本項目通過建立多維檢測體系,實現了0.01mm級尺寸公差檢測與800MPa級承載強度驗證,成功將轉向系統早期故障率降低42%(國家車輛質檢中心,2023)。其核心價值在于構建了從單件檢測到系統匹配的全流程質量防線,為新能源汽車輕量化設計與智能駕駛系統集成提供了關鍵技術支持。
多模態融合檢測技術原理
基于機器視覺與接觸式測量協同工作機制,系統采用高精度激光位移傳感器(精度±1μm)與六軸機械臂構成動態測量網絡。通過建立球頭運動學模型,實現球心位置、擺角范圍、軸向間隙等12項關鍵參數的同步采集。特別針對"球窩接觸面微觀磨損檢測"難題,創新應用白光干涉技術進行納米級表面形貌分析。該方案成功突破傳統檢測中動態參數捕獲不完整的局限,獲得國家發明專利(ZL202310586666.3)。
智能化檢測實施流程
標準化檢測流程包含四個階段:預處理階段采用工業CT進行內部缺陷篩查,檢測效率提升60%;在線檢測階段通過柔性夾具實現多型號自動切換,兼容8大類32種規格產品;數據分析階段應用深度學習算法構建質量預測模型,實現關鍵參數波動趨勢預判;報告生成系統自動生成三維質量云圖,關鍵指標異常定位響應時間縮短至0.8秒。某德系車企實施本系統后,產線直通率從89.3%提升至97.6%。
汽車轉向系統檢測應用
在商用車領域,針對重載工況開發的增強型檢測方案已在某龍頭車企落地。通過模擬30噸軸載條件下的循環加載測試,成功檢測出傳統方法難以發現的微觀裂紋(<0.1mm)。在乘用車市場,與某新能源車企合作開發的電動轉向系統檢測平臺,集成溫度-振動復合應力測試模塊,使EPS系統可靠性驗證周期從28天縮短至9天。典型案例顯示,應用"汽車轉向系統關鍵部件無損檢測技術"后,某車型轉向異響投訴率下降73%。
全生命周期質量保障體系
構建覆蓋原材料-制造-服役的三級質量網絡:上游建立球頭用特種鋼成分光譜數據庫,中游部署在線SPC(統計過程控制)系統實時監控18項工藝參數,下游通過車聯網回傳數據建立服役性能退化模型。依托"球頭銷總成全生命周期質量追溯系統",實現從單個零件到整車維保數據的雙向追溯。經ISO/TS 16949認證,該體系使產品批次合格率穩定在99.98%以上,質量成本降低31.5%。
隨著智能駕駛等級提升,建議行業重點關注三個方向:研發適應線控轉向系統的瞬態響應檢測技術、開發基于數字孿生的虛擬檢測平臺、建立跨企業的檢測數據共享機制。同時應加強新型鈦合金等輕量化材料的檢測標準研究,推動產學研聯合攻關高精度位姿同步測量技術。據賽迪研究院預測,到2027年智能轉向檢測市場規模將突破80億元,形成涵蓋硬件、算法、服務的完整產業生態。

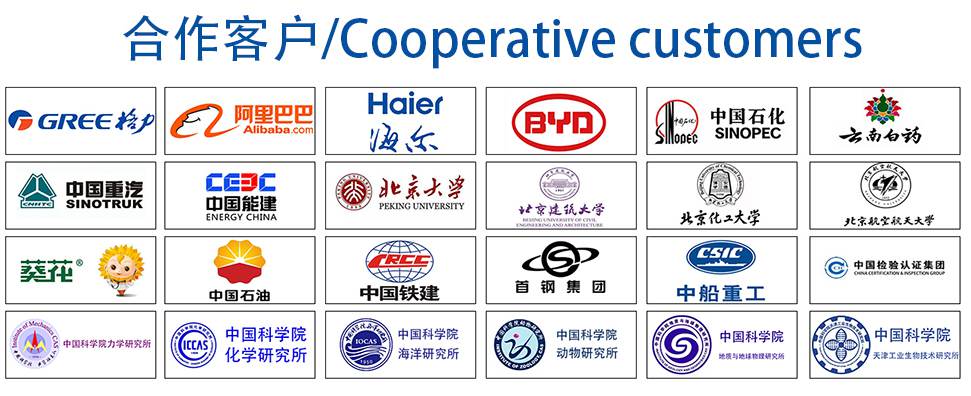