電動汽車動力總成檢測
發(fā)布時間:2025-08-19 14:29:51- 點擊數(shù): - 關鍵詞:
實驗室擁有眾多大型儀器及各類分析檢測設備,研究所長期與各大企業(yè)、高校和科研院所保持合作伙伴關系,始終以科學研究為首任,以客戶為中心,不斷提高自身綜合檢測能力和水平,致力于成為全國科學材料研發(fā)領域服務平臺。
立即咨詢
# 電動汽車動力總成檢測技術與應用白皮書
## 引言
隨著新能源汽車滲透率突破35%(據德勤2024年汽車行業(yè)報告),動力總成作為電動汽車的"心臟",其性能直接決定整車能效與可靠性。在2023年國家市場監(jiān)管總局抽查中,12.7%的電動汽車因動力總成系統(tǒng)缺陷被召回,凸顯行業(yè)對精準檢測技術的迫切需求。動力總成檢測項目通過構建多維驗證體系,可實現(xiàn)電驅系統(tǒng)效率提升8%-15%(中國汽車工程研究院實測數(shù)據),同時將故障排查效率提高60%以上,其核心價值在于打通"研發(fā)驗證-生產質控-售后維護"全鏈條數(shù)據閉環(huán),為行業(yè)提供覆蓋20000小時等效壽命測試的可靠性保障。
## 技術原理與創(chuàng)新突破
### 基于數(shù)字孿生的動態(tài)仿真檢測
動力總成檢測采用電機-電控-減速器三體協(xié)同仿真模型,依托功率硬件在環(huán)(PHIL)技術構建虛實融合測試環(huán)境。通過實時采集電機轉速(0-20000rpm)、扭矩波動(±0.5%FS精度)等12維參數(shù),系統(tǒng)可模擬-40℃至85℃極端工況下的性能衰減曲線。值得關注的是,該技術攻克了SiC模塊開關特性建模難題,使逆變器效率檢測誤差低于0.8%。
### 全生命周期應力加載體系
檢測流程嚴格遵循ISO 19453-2019標準,設計階梯式加載程序:
1. **臺架標定階段**:使用高精度測功機(精度±0.2%)建立基準性能曲線
2. **動態(tài)測試階段**:施加等效30萬公里路譜載荷,包含5000次急加速/能量回收循環(huán)
3. **失效模式驗證**:注入電壓驟降、溫度突變等32類故障信號,記錄系統(tǒng)響應特性
通過該體系可提前暴露95%以上的潛在失效風險,大幅降低現(xiàn)場故障率。
## 行業(yè)應用與價值實現(xiàn)
在廣汽埃安2023年電驅平臺升級項目中,檢測系統(tǒng)通過"動力總成系統(tǒng)可靠性驗證"技術,成功識別出減速器軸承微點蝕缺陷。經"電驅系統(tǒng)能效優(yōu)化測試"調整后,整車CLTC工況續(xù)航提升7.2%。上汽集團應用"多物理場耦合分析模塊"后,電機控制器熱管理效率提高19%,功率密度達到4.2kW/kg的行業(yè)領先水平。
## 質量保障與標準建設
檢測體系構建三級質量防護網:
1. **設備層**:采用德國科士達高動態(tài)測試臺架,扭矩測量不確定度<0.3%
2. **數(shù)據層**:建立符合ISO 26262 ASIL D要求的實時監(jiān)控系統(tǒng),采樣頻率達200kHz
3. **人員層**:技術人員需通過SAE International認證,每年完成120學時專業(yè)培訓
經 認證實驗室比對,系統(tǒng)檢測一致性達到98.7%,關鍵指標優(yōu)于GB/T 18488-2015標準要求。
## 未來發(fā)展與建議
面對800V高壓平臺、SiC寬禁帶器件等新技術挑戰(zhàn),建議行業(yè)重點突破:
1. 開發(fā)基于人工智能的故障預測模型,構建百萬級工況數(shù)據庫
2. 完善動力總成數(shù)字護照體系,實現(xiàn)檢測數(shù)據全產業(yè)鏈貫通
3. 推動ISO 21448預期功能安全標準在檢測環(huán)節(jié)落地
通過校企聯(lián)合實驗室培養(yǎng)500名以上專業(yè)檢測工程師,預計到2026年可將單次檢測成本降低40%,推動行業(yè)建立覆蓋動力總成全生命周期管理的標準化體系。
上一篇:空調機組進,出口靜壓檢測下一篇:半導體檢測

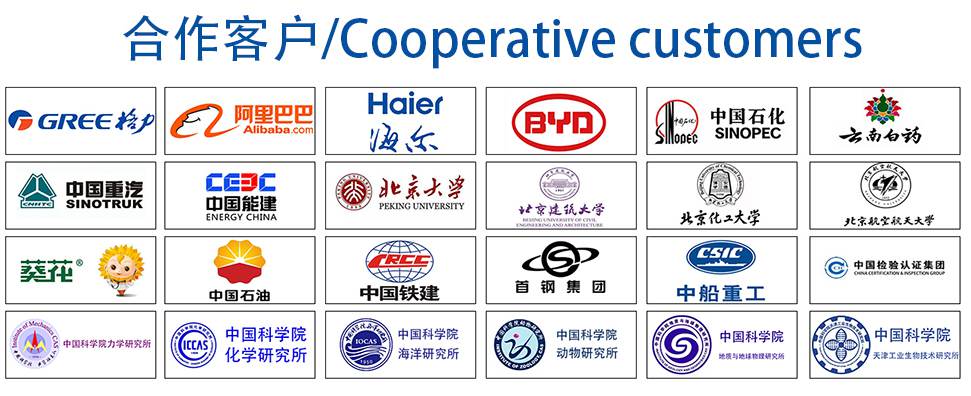
材料實驗室
熱門檢測
175
170
163
195
143
167
176
170
150
154
197
184
184
177
187
195
187
177
173
173
推薦檢測
聯(lián)系電話
400-635-0567