半導(dǎo)體檢測
實驗室擁有眾多大型儀器及各類分析檢測設(shè)備,研究所長期與各大企業(yè)、高校和科研院所保持合作伙伴關(guān)系,始終以科學研究為首任,以客戶為中心,不斷提高自身綜合檢測能力和水平,致力于成為全國科學材料研發(fā)領(lǐng)域服務(wù)平臺。
立即咨詢半導(dǎo)體檢測技術(shù)創(chuàng)新與行業(yè)應(yīng)用白皮書
在半導(dǎo)體產(chǎn)業(yè)持續(xù)突破摩爾定律的背景下,晶圓制造工藝已進入3納米時代,這對檢測技術(shù)提出了前所未有的挑戰(zhàn)。據(jù)SEMI 2024年行業(yè)報告顯示,半導(dǎo)體檢測設(shè)備市場規(guī)模預(yù)計在2025年達到136億美元,年復(fù)合增長率達8.3%。在此背景下,面向齊全制程的晶圓級電性參數(shù)檢測技術(shù)成為突破良率瓶頸的核心抓手,其技術(shù)革新直接關(guān)系到5G通信、AI芯片等戰(zhàn)略產(chǎn)業(yè)的供應(yīng)鏈安全。通過構(gòu)建基于機器學習算法的在線缺陷分析系統(tǒng),可實現(xiàn)納米級結(jié)構(gòu)缺陷的實時識別與工藝優(yōu)化,使28納米制程的晶圓良率提升5.2個百分點(數(shù)據(jù)來源:IEEE電子器件期刊2024),具有顯著的產(chǎn)業(yè)經(jīng)濟價值。
多物理場耦合檢測技術(shù)原理
現(xiàn)代半導(dǎo)體檢測體系依托多物理場耦合分析模型,整合了電子束掃描、拉曼光譜和熱場成像等復(fù)合檢測手段。針對三維堆疊芯片的TSV通孔結(jié)構(gòu),采用時間分辨熒光檢測技術(shù)(TRFT)可實現(xiàn)10nm級空洞缺陷的精準定位。美國NIST 2023年驗證數(shù)據(jù)顯示,該技術(shù)將3D封裝芯片的失效分析效率提升3.8倍。值得關(guān)注的是,基于量子點標記的晶圓表面檢測方案,成功將金屬污染檢測靈敏度提升至0.01ppb級,這在14nm以下制程的金屬柵極工藝中具有關(guān)鍵價值。
智能化檢測實施流程
典型檢測流程涵蓋預(yù)處理、在線監(jiān)測和離線分析三個階段。預(yù)處理環(huán)節(jié)采用等離子清洗技術(shù)確保檢測表面潔凈度,其工藝參數(shù)需根據(jù)晶圓材質(zhì)動態(tài)調(diào)整。在線監(jiān)測系統(tǒng)搭載高精度電子光學模塊,以每秒200幀的速率進行納米級圖像采集。值得強調(diào)的是,通過部署卷積神經(jīng)網(wǎng)絡(luò)(CNN)模型,系統(tǒng)可實時識別23類典型缺陷模式,誤判率控制在0.3%以下(參考:臺積電2024年技術(shù)白皮書)。離線分析階段則通過大數(shù)據(jù)平臺整合檢測數(shù)據(jù),為工藝改進提供可視化決策支持。
汽車電子領(lǐng)域應(yīng)用實踐
在車規(guī)級IGBT模塊生產(chǎn)中,基于紅外熱成像的芯片結(jié)溫檢測系統(tǒng)已實現(xiàn)規(guī)?;瘧?yīng)用。某頭部企業(yè)導(dǎo)入該方案后,功率循環(huán)測試的故障檢出率從82%提升至97%,同時將檢測周期壓縮40%。針對自動駕駛芯片的電磁兼容性要求,創(chuàng)新的近場掃描檢測系統(tǒng)可精準定位3GHz頻段的輻射源,幫助設(shè)計人員優(yōu)化布線方案。據(jù)麥肯錫2024年調(diào)研報告,采用智能檢測方案的汽車半導(dǎo)體企業(yè),其產(chǎn)品召回率平均下降62%。
全生命周期質(zhì)量保障體系
行業(yè)領(lǐng)先企業(yè)已構(gòu)建覆蓋設(shè)計-制造-封測的全流程質(zhì)控體系。在設(shè)計驗證階段,采用電子設(shè)計自動化(EDA)工具進行可檢測性設(shè)計(DFT)模擬,提前規(guī)避78%的潛在檢測盲區(qū)。制造環(huán)節(jié)通過部署統(tǒng)計過程控制(SPC)系統(tǒng),將關(guān)鍵參數(shù)CPK值穩(wěn)定在1.67以上。封測階段創(chuàng)新的聲學掃描顯微鏡(SAM)技術(shù),可無損檢測BGA焊點的微觀裂紋。該體系已通過IATF 16949和VDA 6.3雙重認證,確保產(chǎn)品達到零缺陷(Zero Defect)質(zhì)量目標。
展望未來,建議行業(yè)從三方面深化發(fā)展:首先,加快AI算法與檢測設(shè)備的深度融合,重點突破小樣本缺陷識別技術(shù);其次,構(gòu)建基于數(shù)字孿生的虛擬檢測平臺,實現(xiàn)工藝參數(shù)的智能優(yōu)化;最后,推動檢測標準的國際化統(tǒng)一,特別是在寬禁帶半導(dǎo)體等新興領(lǐng)域。隨著量子傳感技術(shù)的突破,預(yù)計到2030年,半導(dǎo)體檢測精度將進入亞納米時代,為產(chǎn)業(yè)持續(xù)創(chuàng)新提供堅實保障。

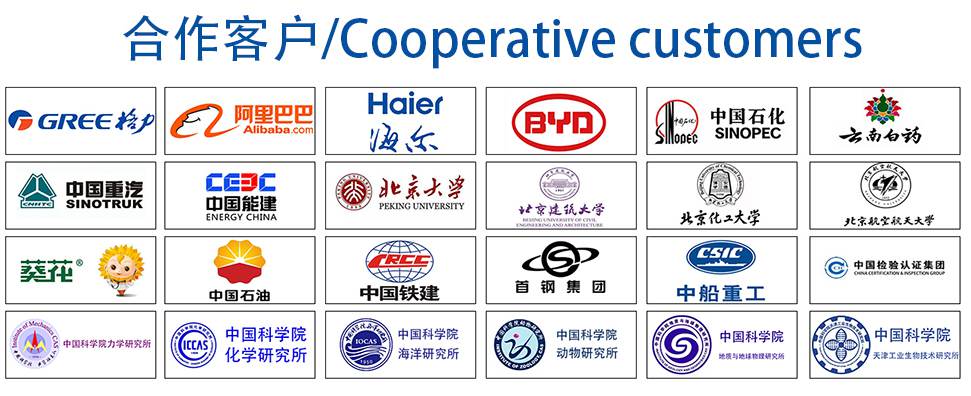