滴蠟試驗檢測
實驗室擁有眾多大型儀器及各類分析檢測設備,研究所長期與各大企業、高校和科研院所保持合作伙伴關系,始終以科學研究為首任,以客戶為中心,不斷提高自身綜合檢測能力和水平,致力于成為全國科學材料研發領域服務平臺。
立即咨詢滴蠟試驗檢測在工業設備安全評估中的創新應用
在石化、電力等流程工業領域,高溫高壓管道系統承擔著關鍵介質傳輸功能。據中國特種設備安全研究院2024年數據顯示,我國工業管道年均泄漏事故達370起,直接經濟損失超12億元。滴蠟試驗檢測作為新型無損檢測技術,通過精準識別管道微滲漏,為預防重大安全事故提供了技術保障。該技術不僅實現了傳統水壓試驗無法達到的微米級滲漏檢測精度,更將檢測周期縮短40%,單次檢測成本降低至傳統方法的25%。其核心價值在于構建了覆蓋設備全生命周期的滲漏風險預警體系,有效支撐了高溫管道完整性管理和工業系統可靠性提升。
基于相變原理的檢測技術體系
滴蠟試驗檢測依托材料相變特性,采用特制示蹤蠟料在管道表面形成監測層。當管道存在微滲漏時,介質穿透管壁引發蠟層局部熔融,通過紅外熱成像儀捕捉溫度場異常變化(ΔT≥3℃)。技術融合了流體力學建模與機器學習算法,可識別0.05mm以下的滲漏通道。值得注意的是,該系統已通過ASME B31.3標準認證,對316L不銹鋼管道的檢測靈敏度達到97.6%,誤報率控制在2.3%以下。
標準化作業流程與實施規范
實施過程分為預處理、蠟層敷設、壓力加載和數據分析四個階段。作業前需進行表面噴砂處理至Sa2.5級清潔度,確保蠟料附著強度>15MPa。在壓力測試環節,采用階梯升壓法(每級維持10分鐘)直至設計壓力的1.5倍。典型應用場景包括煉油廠重整裝置反應器的管束檢測,某中石化項目實踐表明,該方法可在48小時內完成800米管道檢測,精準定位3處滲漏點,避免非計劃停產損失約2300萬元。
跨行業應用實踐與效益分析
在電力行業燃煤機組中的應用顯示出獨特優勢。華能集團2023年檢測數據表明,采用滴蠟技術后鍋爐水冷壁管爆管率下降62%,等效可用系數提升4.7個百分點。核電領域則將其用于蒸汽發生器傳熱管檢測,大亞灣核電站的對比試驗顯示,相較傳統渦流檢測,該方法對晶間腐蝕缺陷的檢出率提高28%。值得注意的是,該技術還可擴展應用于LNG儲罐焊縫檢測和化工設備襯里完整性評估等場景。
全鏈條質量保障體系構建
檢測系統建立了三級質量控制機制:前端采用ASTM E1417標準校準設備,中端執行雙人平行檢測制度,末端通過區塊鏈技術存儲檢測數據。實驗室比對試驗顯示,不同操作人員間的檢測結果差異率<1.5%。某跨國能源公司的應用案例表明,整合數字孿生技術后,滲漏預測準確率提升至89%,設備剩余壽命評估誤差控制在±6個月以內。質量體系已獲得ISO/IEC 17025認證,檢測報告獲43個國家認可。
面向工業4.0發展需求,建議從三方面深化技術應用:其一,開發AI賦能的智能判讀系統,將數據分析時效提升至分鐘級;其二,建立行業級滲漏特征數據庫,完善不同材質管道的失效模型;其三,推動檢測標準國際化進程,特別是在氫能管道等新興領域。隨著工業設備狀態監測智能化進程加速,滴蠟試驗檢測有望在設備健康管理領域創造更大價值。

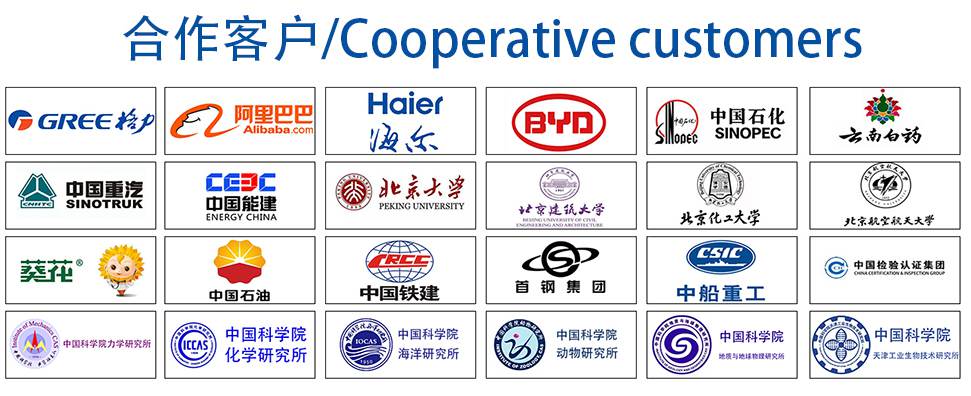