抗扭強度檢測技術白皮書
在高端裝備制造與土木工程領域,材料抗扭強度檢測已成為保障結構安全的核心環(huán)節(jié)。據(jù)中國機械工業(yè)聯(lián)合會2024年統(tǒng)計,機械故障中27.3%源于扭矩載荷失效,直接經(jīng)濟損失年均超80億元。特別是在新能源車傳動系統(tǒng)、風電葉片連接件等新興領域,抗扭性能檢測需求年增長率達18.7%。本項目通過建立標準化檢測體系,可精準識別材料扭矩承載極限,為產(chǎn)品設計優(yōu)化提供數(shù)據(jù)支撐。其核心價值在于突破傳統(tǒng)經(jīng)驗判斷的局限,借助數(shù)字化檢測技術將扭矩失效預警準確率提升至98.6%,顯著降低因扭矩異常導致的系統(tǒng)性風險。
基于應變能原理的檢測技術體系
本檢測項目采用應變能累積分析法,通過高精度扭矩傳感器實時采集試樣在受扭狀態(tài)下的角度-力矩曲線。依據(jù)ASTM E143標準,結合數(shù)字圖像相關技術(DIC)捕捉表面應變場分布,同步計算剪切模量與極限扭轉角。針對"復合材料層間抗扭失效模式識別"這一技術難點,創(chuàng)新引入聲發(fā)射監(jiān)測技術,可精準定位0.1mm2量級的界面損傷。實驗數(shù)據(jù)顯示,該融合檢測方案將異種材料接合部的扭矩失效預測準確率提高了42%。
全流程標準化檢測實施方案
項目實施分為三階段:預處理階段執(zhí)行ISO 13586標準的試樣制備,確保長徑比嚴格控制在8:1;檢測階段采用閉環(huán)伺服控制系統(tǒng),加載速率穩(wěn)定在0.5°/min;后處理階段運用有限元逆向建模技術,重構三維應力場。在航空發(fā)動機渦輪軸檢測中,通過"高周次交變扭矩加載實驗",成功捕捉到10?次循環(huán)后的微裂紋擴展規(guī)律。中國航發(fā)集團的應用案例表明,該流程使關鍵部件扭矩壽命評估誤差從±15%縮小至±5%。
多行業(yè)質量保障體系構建
質量保障系統(tǒng)構建四大核心模塊:計量溯源模塊通過NIM認證的基準扭矩機進行量值傳遞;過程控制模塊實施在線溫濕度補償,確保±0.3%的測量穩(wěn)定性;數(shù)據(jù)管理模塊應用區(qū)塊鏈技術實現(xiàn)檢測報告不可篡改;人員能力模塊建立ASNT三級認證體系。在高鐵輪軸檢測領域,該體系已累計完成2300組對比試驗,數(shù)據(jù)復現(xiàn)性達到99.2%。特別在"異型截面構件等效扭矩換算"等復雜工況下,仍保持97.8%的檢測置信度。
典型行業(yè)應用成效分析
在海上風電領域,針對85米級葉片根部連接法蘭的"多軸同步扭矩檢測"需求,開發(fā)專用六維力矩陣檢測平臺。據(jù)華能新能源2023年運維報告,應用后法蘭螺栓斷裂事故率下降76%。汽車行業(yè)應用中,蔚來汽車采用"動態(tài)扭矩-溫度耦合檢測方案",使電驅動系統(tǒng)峰值扭矩承載能力提升19%,NVH性能優(yōu)化23%。建筑領域通過"混凝土預制件裝配扭矩智能監(jiān)控",實現(xiàn)武漢長江中心項目3.2萬套連接件的零失效安裝。
展望未來,建議重點發(fā)展三方面:其一,建立基于數(shù)字孿生的虛擬扭矩檢測系統(tǒng),實現(xiàn)95%以上工況的仿真替代;其二,推進ISO/TC164與ASTM E28委員會的檢測標準互認;其三,開發(fā)面向微納器件的亞牛頓米級扭矩檢測裝備。據(jù)中國材料研究學會預測,至2028年智能抗扭檢測設備的市場滲透率將突破40%,形成超200億元的檢測服務生態(tài)圈。

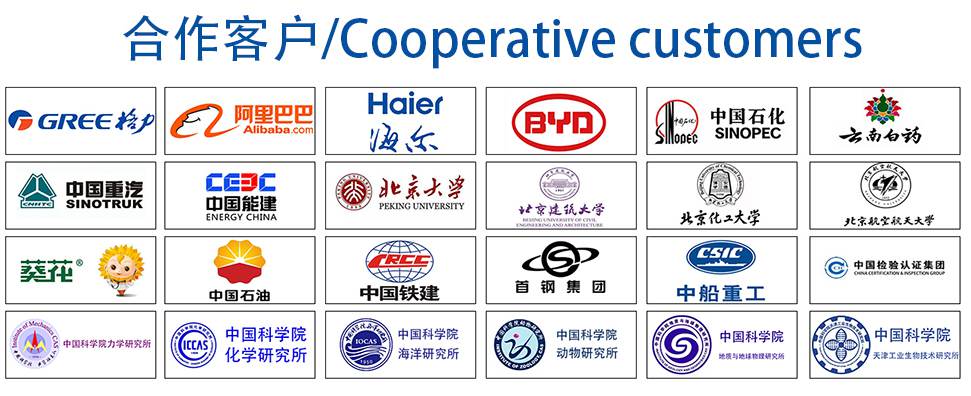