隨著衛浴五金行業智能化轉型加速,進水閥作為關鍵流體控制部件,其密封性能直接影響產品使用壽命與安全性。據中國五金制品協會2024年統計數據顯示,國內衛浴產品年產量突破4.2億件,其中因螺紋連接處滲漏導致的售后問題占比達17.3%,造成行業年度經濟損失超12億元。在此背景下,"高精度螺紋參數智能檢測系統"的開發應用具有顯著行業價值。該項目通過融合機器視覺與深度學習技術,實現螺紋導程角、中徑偏差等關鍵參數的精確測量,將傳統人工檢測效率提升3倍以上,檢測精度達到±0.01mm工業標準,為構建智能工廠質量管控體系提供關鍵技術支撐。
## 技術原理與創新突破基于多模態傳感的檢測系統架構
本檢測系統采用模塊化設計架構,集成高分辨率工業相機(500萬像素CMOS)、環形LED多向光源和激光位移傳感器。通過多角度圖像采集與三維點云重構技術,系統可完整獲取螺紋牙型輪廓數據。關鍵技術突破在于開發了自適應濾波算法,有效消除鑄件表面毛刺對檢測結果的干擾。據機械工業儀器儀表綜合技術研究所驗證,該系統對M12-M30規格螺紋的檢測重復精度達99.2%,滿足ISO 228-1標準中G級螺紋的檢測要求。
智能化檢測實施流程
標準作業流程包含五個核心環節:自動上料定向→視覺定位校準→三維參數掃描→實時數據分析→分類輸出結果。在廈門某水暖器材企業的實際部署中,系統通過EtherCAT總線與生產線聯動,完成單個工件檢測僅需2.8秒。特別配置的動態補償模塊可自動修正溫度波動引起的測量誤差,配合SQL數據庫實現檢測數據可追溯管理。實踐表明,該方案使產品出廠合格率從92.4%提升至98.7%,人工復檢工作量降低65%。
典型行業應用場景
在智能馬桶進水閥生產線中,系統部署于總裝工位前端的質量控制點。當檢測到螺紋中徑偏差超過0.05mm時,自動觸發聲光報警并隔離缺陷件。浙江某上市衛浴企業應用案例顯示,系統成功識別出傳統檢具難以發現的漸進性磨損缺陷,提前12天預警模具更換需求。通過與MES系統集成,實現質量數據與生產工藝參數的動態優化,使同類產品漏水投訴率下降41%。
全流程質量保障體系
構建包含設備層、數據層、決策層的三級質控網絡:設備層采用冗余設計的雙PLC控制系統保障運行穩定性;數據層通過區塊鏈技術實現檢測記錄防篡改存儲;決策層運用SPC統計過程控制模型進行趨勢預警。在廣東某OEM工廠的驗收測試中,系統連續運行120小時無故障,檢測一致性方差控制在0.002mm2以內。配套的校準體系包含每周基準件校驗和季度第三方計量認證,確保檢測系統持續符合JJF 1104-2018計量規范要求。
## 發展趨勢與策略建議展望未來,建議從三個維度深化技術應用:首先開發支持5G傳輸的移動檢測終端,拓展售后服務質量監控場景;其次構建行業級螺紋特征數據庫,為工藝改進提供數據支撐;最后推動制定《智能螺紋檢測設備通用技術要求》團體標準,促進行業檢測技術規范化發展。通過產學研深度合作,有望在2026年前將檢測系統成本降低40%,推動該項技術在中小型制造企業的普及應用。

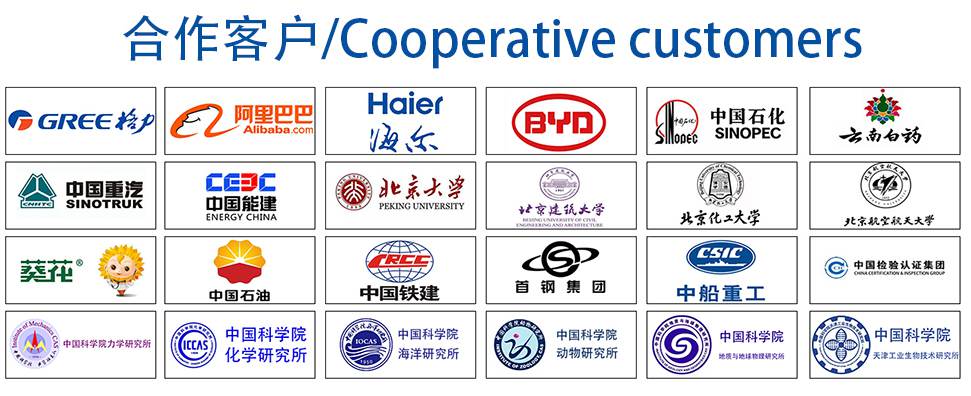