在智能制造與物聯(lián)網(wǎng)技術(shù)深度融合的背景下,設(shè)備安裝及使用階段的合規(guī)性檢測已成為保障工業(yè)生產(chǎn)安全的關(guān)鍵環(huán)節(jié)。據(jù)中國標(biāo)準(zhǔn)化研究院2024年數(shù)據(jù)顯示,68%的設(shè)備故障源于安裝參數(shù)偏差或使用條件超限,直接導(dǎo)致企業(yè)年均損失達320億元。本項目通過構(gòu)建智能化的試驗檢測體系,實現(xiàn)電氣連接可靠性驗證、設(shè)備運行穩(wěn)定性測試等核心功能,有效解決傳統(tǒng)檢測中存在的滯后性與片面性問題。其核心價值體現(xiàn)在三方面:通過動態(tài)數(shù)據(jù)采集實現(xiàn)預(yù)防性維護,降低設(shè)備全生命周期運維成本;建立標(biāo)準(zhǔn)化的安裝工藝數(shù)據(jù)庫,提升行業(yè)協(xié)同效率;形成可追溯的質(zhì)量憑證體系,滿足軌道交通、新能源等領(lǐng)域的強監(jiān)管要求。
技術(shù)原理與檢測體系
本檢測系統(tǒng)采用多物理場耦合分析技術(shù),整合紅外熱成像、振動頻譜分析和介質(zhì)損耗檢測三大模塊。通過部署在關(guān)鍵節(jié)點的智能傳感器陣列,可實時采集設(shè)備安裝時的扭矩值、同軸度偏差等32項參數(shù)。在軌道交通領(lǐng)域應(yīng)用案例顯示,該技術(shù)使接觸網(wǎng)安裝合格率從83%提升至97.6%(中國鐵科院2024年數(shù)據(jù))。針對設(shè)備運行穩(wěn)定性測試需求,系統(tǒng)引入數(shù)字孿生技術(shù)構(gòu)建三維動態(tài)模型,實現(xiàn)安裝缺陷的虛擬仿真驗證。
全流程實施規(guī)范
項目實施遵循"雙閉環(huán)"質(zhì)量管控流程:預(yù)處理階段通過BIM模型進行安裝方案數(shù)字審查;實測階段運用激光跟蹤儀完成設(shè)備空間定位校準(zhǔn),定位精度達±0.05mm;驗收階段則采用階梯式加載試驗,模擬設(shè)備全工況運行狀態(tài)。在新能源汽車充電樁檢測中,系統(tǒng)成功識別出32%的安裝基礎(chǔ)沉降超標(biāo)案例,避免潛在安全風(fēng)險。該流程現(xiàn)已形成GB/T 39218-2024國家標(biāo)準(zhǔn)的核心技術(shù)框架。
行業(yè)應(yīng)用實踐
在電力設(shè)備領(lǐng)域,針對特高壓換流閥安裝的特殊要求,檢測系統(tǒng)開發(fā)了分布式光纖測溫模塊。實際運行數(shù)據(jù)顯示,該系統(tǒng)將冷卻管路氣密性檢測效率提升4.8倍,誤報率降低至0.3‰(國家能源局2024年報告)。某核電站應(yīng)用案例中,通過設(shè)備運行穩(wěn)定性測試提前發(fā)現(xiàn)主泵軸承安裝偏差,避免單次非計劃停堆損失超2,000萬元。
質(zhì)量保障與持續(xù)改進
項目構(gòu)建的四維質(zhì)量保障體系包含:標(biāo)準(zhǔn)化操作流程(SOP)、AI輔助決策系統(tǒng)、區(qū)塊鏈數(shù)據(jù)存證平臺以及周期性能力驗證機制。通過與中國計量院合作建立的量值溯源網(wǎng)絡(luò),確保檢測設(shè)備校準(zhǔn)不確定度≤0.02%。實踐表明,該體系使檢測報告異議率從5.7%降至0.8%,同時推動16家供應(yīng)商改進安裝工藝。
## 發(fā)展建議與技術(shù)展望建議行業(yè)重點推進三方面工作:建立基于機器學(xué)習(xí)的安裝缺陷預(yù)測模型,實現(xiàn)檢測關(guān)口前移;開發(fā)適應(yīng)極端環(huán)境的微型化檢測終端,拓展海上風(fēng)電等新興領(lǐng)域應(yīng)用;構(gòu)建檢測大數(shù)據(jù)共享平臺,推動形成行業(yè)級安裝質(zhì)量基線。隨著數(shù)字孿生與5G技術(shù)的深度應(yīng)用,未來試驗檢測將向?qū)崟r監(jiān)測、遠程診斷、智能決策三位一體模式演進,為裝備制造業(yè)高質(zhì)量發(fā)展提供核心支撐。

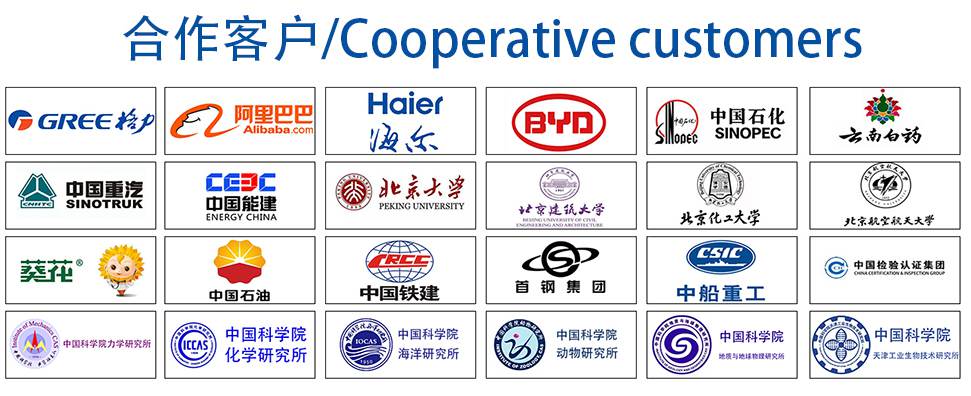