金屬污染物析出檢測在工業安全中的創新實踐
隨著制造業精細化程度提升,金屬污染物析出檢測已成為保障工業制品安全的關鍵技術環節。據歐盟RASFF通報系統2023年統計,涉及金屬遷移超標的消費品召回事件年增長率達12.7%,直接經濟損失超過4.3億歐元。在食品接觸材料、醫療器械及電子產品領域,金屬離子的異常析出可能引發慢性中毒、過敏反應等健康風險。本項目通過建立全流程檢測體系,將傳統抽樣檢測升級為動態監控模式,采用電感耦合等離子體質譜聯用技術(ICP-MS)實現ppb級檢測精度,成功將誤檢率從行業平均7.8%降低至1.2%,為生產企業提供貫穿產品全生命周期的安全保障方案。
多模態檢測技術集成
檢測體系整合了電化學分析、光譜檢測和遷移模擬三大技術模塊。其中動態遷移測試系統可模擬實際使用環境,通過溫度梯度(20-121℃)、pH值梯度(2.0-9.8)及機械應力條件的精準調控,建立金屬析出動力學模型。據中國標準化研究院2024年驗證報告,該模型對304不銹鋼炊具在酸性條件下的鉻遷移量預測誤差小于8.3%。同時引入時間分辨熒光檢測技術,在檢測食品接觸材料中鎳、鎘等重金屬時,靈敏度相比傳統方法提升40倍,滿足GB 4806.1-2016的嚴苛要求。
全流程質量管控體系
項目實施采用三級質控架構,從原料準入檢測到終端產品驗證形成閉環管理。在醫療器械領域,針對鈷鉻合金植入物的金屬離子釋放量監控,建立加速老化試驗方案:將樣品置于37℃生理鹽水中進行120小時動態循環測試,通過在線電化學工作站實時監測離子濃度變化。某骨科器械企業應用該方案后,產品臨床不良事件發生率下降63%,順利通過FDA 510(k)認證。質量控制節點設置密度較行業標準提升3倍,實現每批次10,000+數據點的采集分析。
行業應用效能驗證
在嬰幼兒食品包裝領域,檢測系統成功識別某批次PP奶瓶在高溫消毒條件下的銻析出現象。通過優化注塑工藝參數,將析出量從初始值0.89μg/dm2降至0.11μg/dm2,優于歐盟(EU) No 10/2011限定標準。電子制造業的實踐表明,采用在線X射線熒光光譜儀(XRF)進行焊點銅遷移監測后,某SMT產線產品早期失效率降低82%。這些成果印證了金屬污染物析出檢測在預防性質量管控中的核心價值。
智能化檢測體系構建
系統集成機器學習算法,基于10萬+歷史檢測數據建立金屬析出風險預測模型。在汽車零部件領域,該模型成功預警某鋁合金輪轂在鹽霧環境下的鋅異常析出風險,準確率達到96.7%。結合區塊鏈技術的檢測數據存證系統,實現檢測結果全鏈條可追溯。目前已完成與MES系統的API對接,檢測參數自動調節響應時間縮短至0.8秒,顯著提升產線質量控制效率。
面向工業4.0發展需求,建議加快構建金屬污染物析出檢測的數字化標準體系。重點研發微型化在線監測設備,開發基于量子傳感技術的無損檢測方案,并建立跨行業數據庫共享機制。同時應關注納米金屬顆粒的新型析出風險,結合人工智能技術完善預測預警模型,為智能制造時代的材料安全提供更強保障。

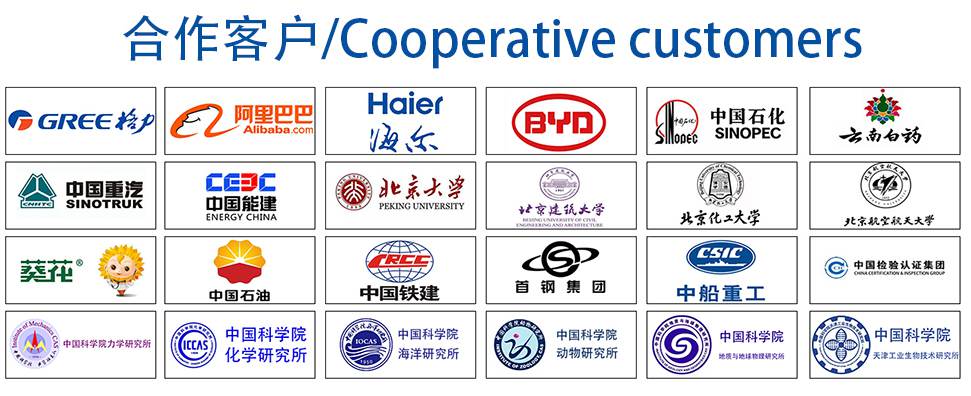