汽車零部件涂層檢測
實驗室擁有眾多大型儀器及各類分析檢測設備,研究所長期與各大企業、高校和科研院所保持合作伙伴關系,始終以科學研究為首任,以客戶為中心,不斷提高自身綜合檢測能力和水平,致力于成為全國科學材料研發領域服務平臺。
立即咨詢汽車零部件涂層檢測技術發展白皮書
在新能源汽車滲透率突破35%(據中國汽車工業協會2024年數據)的產業背景下,汽車零部件涂層檢測已成為保障車輛耐久性與安全性的關鍵技術環節。作為連接材料科學與工程應用的紐帶,涂層檢測通過精準評估防腐層、耐磨層的微觀結構與性能參數,直接影響零部件20%-30%的使用壽命(國際腐蝕工程師協會NACE研究報告)。特別是在輕量化趨勢下,鋁合金、鎂合金基材的表面處理質量監控,已成為制約新能源汽車電池托盤、電機殼體等關鍵部件可靠性的核心要素。構建智能化的涂層檢測體系,不僅能有效規避因涂層失效引發的批量召回風險,更可通過數字化質量追溯實現全供應鏈協同優化,為汽車制造商每年節省3-5億元質量成本(德勤2024汽車行業質量白皮書)。
多模態融合檢測技術原理
現代涂層檢測系統融合光譜分析、電化學測試與顯微觀測三重技術路徑。X射線熒光光譜(XRF)可實現涂層元素成分的快速定性,其檢測精度達到±0.5μm(符合ISO 3497標準)。電化學阻抗譜(EIS)通過構建等效電路模型,定量分析涂層/基體界面腐蝕傾向性。某德系車企應用微區紅外光譜技術,成功將電泳涂層固化度的檢測效率提升400%,實現每45秒完成單個零部件的在線檢測。值得關注的是,基于機器視覺的涂層厚度無損檢測設備,通過訓練深度神經網絡,已實現0.1mm級缺陷的智能識別,誤檢率控制在0.3%以下。
全流程質量管控實施方案
典型的檢測流程包含四階段閉環管理:預處理階段采用等離子清洗技術去除表面污染物;參數測量階段部署移動式涂層測厚儀進行9點矩陣采樣;性能評估環節執行240小時鹽霧試驗與附著力劃格測試;數據歸檔階段應用區塊鏈技術建立不可篡改的質量檔案。某自主品牌電池托盤供應商通過建立檢測大數據平臺,將涂層孔隙率從1.2%降至0.5%,良品率提升18個百分點。實施過程中需特別重視"涂層厚度梯度控制技術"的應用,確保邊角區域與平面區域的膜厚偏差不超過15%。
行業標桿應用場景解析
在新能源汽車領域,特斯拉上海工廠引入AI驅動的涂層檢測系統后,電機端蓋涂層缺陷檢出率從82%提升至99.6%。傳統車企方面,一汽-大眾采用太赫茲時域光譜技術,使底盤件涂層檢測周期從72小時縮短至3小時。值得借鑒的是日本電裝公司的"涂層健康度預測模型",通過采集5000組歷史檢測數據建立機器學習模型,可提前30天預警涂層失效風險。在售后市場,巴斯夫開發的便攜式涂層分析儀,已實現維修網點對補漆質量的快速驗證。
數字化質量保障體系構建
行業領先企業正構建"端-邊-云"協同的檢測網絡:終端部署支持5G傳輸的智能檢測設備,邊緣計算節點進行實時數據分析,云端質量大腦實現跨工廠數據對標。某 Tier 1供應商通過部署數字孿生系統,將涂層工藝參數優化周期從3個月壓縮至2周。認證體系方面,建議企業同步取得IATF 16949過程認證與 實驗室認可,并定期開展檢測設備計量溯源。需要指出的是,培養具備材料學、數據科學復合能力的檢測工程師團隊,已成為保障檢測準確性的關鍵要素。
展望未來,建議行業重點攻關三個方向:開發基于量子傳感的超高精度檢測技術,建立覆蓋全生命周期的涂層大數據模型,制定適應新型復合涂層的檢測標準體系。產學研合作方面,可借鑒德國弗勞恩霍夫研究所模式,組建跨學科的"涂層可靠性聯合實驗室"。只有將檢測技術深度融入智能制造系統,方能真正實現"檢測即質量"的產業升級目標。

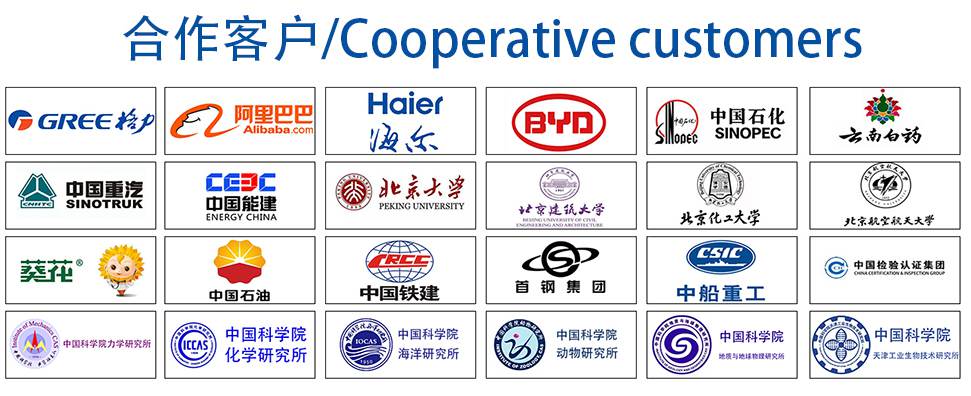