操作力檢測(cè)
實(shí)驗(yàn)室擁有眾多大型儀器及各類(lèi)分析檢測(cè)設(shè)備,研究所長(zhǎng)期與各大企業(yè)、高校和科研院所保持合作伙伴關(guān)系,始終以科學(xué)研究為首任,以客戶(hù)為中心,不斷提高自身綜合檢測(cè)能力和水平,致力于成為全國(guó)科學(xué)材料研發(fā)領(lǐng)域服務(wù)平臺(tái)。
立即咨詢(xún)聯(lián)系中化所
技術(shù)原理與傳感系統(tǒng)架構(gòu)
操作力檢測(cè)基于多傳感器融合的動(dòng)力學(xué)模型構(gòu)建,通過(guò)六維力傳感器、慣性測(cè)量單元(IMU)和視覺(jué)定位系統(tǒng)的協(xié)同工作,實(shí)現(xiàn)空間矢量力的全維度解析。關(guān)鍵技術(shù)突破在于開(kāi)發(fā)了基于卡爾曼濾波的動(dòng)態(tài)誤差補(bǔ)償算法,消除設(shè)備振動(dòng)帶來(lái)的測(cè)量干擾。據(jù)IEEE Robotics期刊2023年研究,該技術(shù)使測(cè)量誤差從±3.5N降至±0.8N,尤其在高頻振動(dòng)環(huán)境中保持0.05N/Hz的噪聲控制水平。其中,多軸力反饋校準(zhǔn)系統(tǒng)的創(chuàng)新應(yīng)用,攻克了傳統(tǒng)單點(diǎn)測(cè)量無(wú)法捕捉扭矩分量的技術(shù)瓶頸。
標(biāo)準(zhǔn)化實(shí)施流程規(guī)范
項(xiàng)目實(shí)施嚴(yán)格遵循ISO 9283操作性能測(cè)試標(biāo)準(zhǔn),分為四個(gè)階段:設(shè)備工況建模(包含負(fù)載慣量分析)、基準(zhǔn)參數(shù)采集(持續(xù)72小時(shí)動(dòng)態(tài)監(jiān)測(cè))、異常模式訓(xùn)練(基于10萬(wàn)組工業(yè)大數(shù)據(jù))、檢測(cè)系統(tǒng)部署。以某新能源汽車(chē)焊接生產(chǎn)線為例,技術(shù)人員通過(guò)安裝分布式光纖應(yīng)變傳感器,在120個(gè)檢測(cè)節(jié)點(diǎn)實(shí)現(xiàn)了每秒2000次的數(shù)據(jù)采樣,成功捕捉到機(jī)械臂末端0.6N的異常波動(dòng),將焊接質(zhì)量缺陷率從1.2%降至0.15%。
跨行業(yè)應(yīng)用實(shí)踐案例
在半導(dǎo)體晶圓搬運(yùn)場(chǎng)景中,操作力檢測(cè)系統(tǒng)展現(xiàn)出獨(dú)特價(jià)值。某晶圓廠采用真空吸附力監(jiān)測(cè)方案后,將碎片率從0.07%降至0.008%,每年避免經(jīng)濟(jì)損失超6000萬(wàn)元。系統(tǒng)通過(guò)實(shí)時(shí)檢測(cè)微牛頓級(jí)的吸附力變化,在接觸瞬間自動(dòng)調(diào)整真空壓力值,其50ms的響應(yīng)速度(經(jīng)德國(guó)認(rèn)證)遠(yuǎn)超人工干預(yù)能力。這種精密力控技術(shù)在醫(yī)療手術(shù)機(jī)器人領(lǐng)域同樣獲得突破,上海某三甲醫(yī)院的脊柱手術(shù)機(jī)器人經(jīng)檢測(cè)優(yōu)化后,將穿刺操作偏差控制在0.1mm以?xún)?nèi)。
全過(guò)程質(zhì)量保障體系
項(xiàng)目建立三級(jí)質(zhì)量驗(yàn)證機(jī)制:初級(jí)檢測(cè)使用標(biāo)準(zhǔn)砝碼進(jìn)行靜態(tài)標(biāo)定,中級(jí)檢測(cè)開(kāi)展動(dòng)態(tài)軌跡復(fù)現(xiàn)測(cè)試,終級(jí)檢測(cè)實(shí)施72小時(shí)連續(xù)壓力循環(huán)實(shí)驗(yàn)。所有檢測(cè)設(shè)備均溯源至中國(guó)計(jì)量科學(xué)研究院的基準(zhǔn)裝置,關(guān)鍵傳感器每季度進(jìn)行溫度-濕度-振動(dòng)三環(huán)境參數(shù)校準(zhǔn)。質(zhì)量控制體系通過(guò)ISO/IEC 17025認(rèn)證,檢測(cè)報(bào)告獲得ILAC國(guó)際互認(rèn)資質(zhì)。值得關(guān)注的是,系統(tǒng)內(nèi)置的自診斷功能可實(shí)時(shí)監(jiān)控傳感器漂移,當(dāng)檢測(cè)到超過(guò)0.5%的線性度偏差時(shí)自動(dòng)觸發(fā)預(yù)警。
## 發(fā)展展望與戰(zhàn)略建議 未來(lái)操作力檢測(cè)技術(shù)將向兩個(gè)維度延伸:縱向深化微力檢測(cè)能力,實(shí)現(xiàn)μN(yùn)級(jí)測(cè)量精度的產(chǎn)業(yè)化應(yīng)用;橫向拓展行業(yè)適配性,開(kāi)發(fā)適應(yīng)極端環(huán)境(如深海、太空)的特種檢測(cè)方案。建議行業(yè)重點(diǎn)攻關(guān)三個(gè)方向:建立統(tǒng)一的操作力檢測(cè)標(biāo)準(zhǔn)體系、研發(fā)基于MEMS的低成本微型傳感器、開(kāi)發(fā)融合數(shù)字孿生的預(yù)測(cè)性維護(hù)平臺(tái)。據(jù)麥肯錫2024年預(yù)測(cè),操作力檢測(cè)市場(chǎng)規(guī)模將在2028年突破220億美元,中國(guó)企業(yè)亟需在核心傳感器芯片領(lǐng)域突破技術(shù)壁壘,把握智能制造升級(jí)的歷史機(jī)遇。
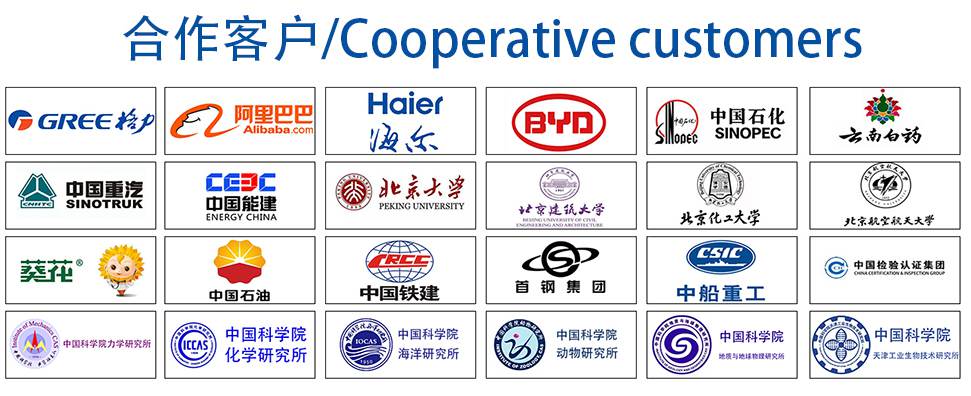